In the realm of industrial automation, Programmable Logic Controllers (PLCs) serve as the backbone of modern manufacturing processes, facilitating the efficient and precise control of various industrial operations. Central to the functionality of PLCs are sensors and actuators, which collectively form the vital bridge between the digital realm of control systems and the physical world of machinery and processes.
This introduction aims to delve into the fundamental concepts of interfacing PLCs with sensors and actuators, elucidating the critical role they play in industrial automation. As industries continue to adopt advanced automation solutions, understanding how these components collaborate within a PLC framework becomes increasingly essential.
Types of Sensors and Their Interfaces
Sensors are the essential components that provide the necessary input data to a Programmable Logic Controller (PLC) for making informed decisions and executing control actions. Different types of sensors are used to measure various physical parameters, and each type comes with its own interface methods for transmitting data to the PLC. Here, we explore some common types of sensors and their interfaces:
**1. Temperature Sensors: Temperature sensors measure the thermal condition of a system. They can be of various types such as thermocouples, resistance temperature detectors (RTDs), and thermistors. Thermocouples generate a voltage proportional to the temperature difference between two junctions, while RTDs use the change in electrical resistance of a metal wire with temperature. Thermistors, on the other hand, have resistance that varies significantly with temperature.
Interface Methods:
- Analog Voltage: Many temperature sensors provide analog voltage outputs that can be directly connected to analog input modules of a PLC. The PLC converts the analog voltage into a digital value using an analog-to-digital converter (ADC).
- 4-20 mA Current Loop: Sensors can also use a current loop interface, where the current in the loop represents the temperature. The current can be converted to a digital value using a current-to-digital converter.
2. Pressure Sensors: Pressure sensors measure the pressure of gases or liquids. They are used in various applications such as monitoring fluid levels, controlling hydraulic systems, and more.
Interface Methods:
- Analog Voltage or Current: Similar to temperature sensors, pressure sensors often provide analog outputs that can be interfaced using analog input modules.
- Digital Communication: Some advanced pressure sensors use digital communication protocols like I2C, SPI, or Modbus to directly send pressure readings to the PLC.
3. Proximity Sensors: Proximity sensors detect the presence or absence of an object without physical contact. They are widely used in manufacturing automation for tasks like object detection, position sensing, and more.
Interface Methods:
- Digital Signals: Proximity sensors generally provide digital outputs, which can be connected to digital input modules on the PLC. These sensors output either a high or low signal based on the presence or absence of an object.
4. Photoelectric Sensors: Photoelectric sensors use light beams to detect objects. They consist of a light emitter and a receiver and are commonly used for detecting object positions, counting items on a conveyor belt, and more.
Interface Methods:
- Digital Signals: Photoelectric sensors also provide digital outputs that can be interfaced using digital input modules on the PLC. The output indicates whether the light beam is blocked or not.
5. Position Sensors: Position sensors determine the precise location of an object. They are crucial for controlling robotic arms, conveyor systems, and other mechanisms requiring accurate positioning.
Interface Methods:
- Analog Voltage: Some position sensors provide analog voltage outputs proportional to the position. These outputs can be connected to analog input modules on the PLC.
- Digital Pulse or Encoder: Rotary encoders or linear position sensors provide digital pulses based on the position. PLCs can count these pulses to determine the position accurately.
In conclusion, different types of sensors have varying interface methods, depending on the nature of their output signals. PLCs are designed to accommodate these diverse sensor interfaces, allowing industries to efficiently gather data and implement precise control strategies for various industrial processes.
Actuators and Their Control through PLCs
Actuators are vital components in industrial automation that execute control commands based on signals from Programmable Logic Controllers (PLCs). They are responsible for transforming digital instructions into physical actions, enabling the manipulation of machinery, processes, and systems. Here, we explore different types of actuators and how they are controlled through PLCs:
1. Electric Motors: Electric motors are one of the most common types of actuators used in industrial applications. They convert electrical energy into mechanical motion and are widely used for tasks such as driving conveyor belts, rotating equipment, and controlling pumps.
Control through PLCs: PLCs can control electric motors using output modules. By sending appropriate signals to the output modules, the PLC can start, stop, and even reverse the motor’s direction. Speed control can be achieved by adjusting the frequency or voltage of the supplied power.
2. Pneumatic Actuators: Pneumatic actuators use compressed air to generate motion. They are used in applications where rapid and forceful movements are required, such as in pneumatic cylinders for robotic arms or for opening and closing valves.
Control through PLCs: PLCs control pneumatic actuators by sending signals to solenoid valves. These valves regulate the flow of compressed air to the actuator, determining its position or movement. PLCs can precisely control the timing and duration of air flow to achieve the desired motion.
3. Hydraulic Actuators: Hydraulic actuators use pressurized fluid to generate motion. They are known for their ability to provide high force output and are used in heavy-duty applications like heavy machinery and construction equipment.
Control through PLCs: Similar to pneumatic actuators, hydraulic actuators are controlled through solenoid valves that regulate the flow of hydraulic fluid. The PLC sends signals to these valves to control the actuator’s motion and position.
4. Servo Motors: Servo motors are high-precision electric motors that provide accurate control over position, speed, and torque. They are commonly used in applications requiring precise positioning, such as CNC machines, robotics, and automated assembly lines.
Control through PLCs: PLCs control servo motors using specialized output modules that generate pulse-width modulation (PWM) signals. These signals communicate the desired position and speed to the servo motor’s controller, which adjusts the motor accordingly.
5. Solenoids: Solenoids are electromechanical devices that generate linear motion when an electrical current passes through them. They are used in applications like valve control, door locking systems, and more.
Control through PLCs: PLCs can control solenoids by supplying the appropriate voltage to activate them. By controlling the timing and duration of the voltage supply, PLCs determine the on/off state of the solenoid, thus achieving the desired action.
Actuators are crucial for translating the digital instructions of a PLC into physical movements, thereby enabling automation in various industries. The versatility of actuators allows industries to create complex and efficient control systems that enhance productivity, precision, and safety. PLCs serve as the brains behind these systems, orchestrating the actions of actuators based on input data from sensors, and in doing so, revolutionizing industrial processes and manufacturing.
PLC Inputs and Signal Processing
In the realm of industrial automation, Programmable Logic Controllers (PLCs) serve as the nerve center, receiving input data from various sensors, processing that data, and triggering appropriate control actions through connected actuators. Understanding how PLC inputs work and how signal processing is performed is essential for designing efficient and reliable automated systems.
PLC Inputs: Connecting to the Physical World PLC inputs are the interfaces through which the controller interacts with the physical environment. These inputs are connected to various sensors that monitor conditions such as temperature, pressure, position, presence of objects, and more. PLCs must be able to process these inputs effectively to make informed decisions about the operation of the system.
Signal Types: Digital and Analog PLC inputs primarily deal with two types of signals: digital and analog. Digital signals are binary in nature, representing either a high (1) or low (0) state. They are used to indicate the presence or absence of an event or condition. Analog signals, on the other hand, provide continuous data that varies within a range, like temperature or pressure readings.
Signal Conditioning: Preparing Inputs for Processing Before PLCs can process input signals, they often undergo a process called signal conditioning. This involves shaping, filtering, and scaling the raw sensor signals to ensure accuracy and compatibility with the PLC’s input circuitry.
Digital Signal Processing: Digital signals, being binary, require minimal processing. PLCs read digital inputs directly from sensors, switches, or other devices. These inputs can trigger immediate actions, such as starting or stopping a motor or changing the state of a valve. Debouncing circuits are sometimes used to filter out any electrical noise that can cause false triggers from mechanical switches.
Analog Signal Processing: Analog signals require more complex processing due to their continuous nature. PLCs use analog-to-digital converters (ADCs) to convert analog signals into digital values that the controller can understand. The precision of the ADC affects the accuracy of measurements. Once converted, the digital value is scaled to match the actual physical measurement using programming within the PLC.
Sampling and Resolution: Analog signals are not continuous in digital systems; they are sampled at regular intervals. The frequency of sampling affects the accuracy and responsiveness of the measurements. The resolution of the ADC determines the smallest change in the input signal that can be detected by the PLC.
Data Filtering and Noise Reduction: In industrial environments, electrical noise can interfere with accurate sensor readings. PLCs often employ filtering techniques to remove noise from analog signals. Low-pass filters, for instance, attenuate high-frequency noise while preserving the relevant signal.
Signal Validation and Thresholds: Before making decisions based on input signals, PLCs may apply validation checks. For example, temperature readings that fall outside acceptable ranges might trigger alarms or shutdown procedures. The PLC compares the input value against predefined thresholds to determine whether an action is needed.
PLC inputs and signal processing form the foundation of industrial automation. The ability to accurately receive, condition, and process input data from various sensors is crucial for making informed decisions and executing precise control actions. As industries continue to advance in automation, PLCs will continue to play a pivotal role in managing and optimizing complex industrial processes.
PLC Outputs and Actuation Control
In industrial automation, the role of Programmable Logic Controllers (PLCs) goes beyond just processing input data; they also play a critical role in controlling and coordinating output devices known as actuators. PLC outputs are the pathways through which the controller commands actuators to perform specific actions, enabling the automation of various processes. Understanding PLC outputs and their role in actuation control is essential for designing effective and efficient automated systems.
PLC Outputs: Driving Actuators PLC outputs are the interfaces through which the controller sends commands to actuators. These outputs are connected to devices like motors, solenoids, valves, and relays. When the PLC receives input data and processes it, it generates appropriate control signals on its output channels to actuate these devices.
Types of PLC Outputs: Digital and Analog Similar to inputs, PLC outputs can be categorized into digital and analog types. Digital outputs provide binary control, enabling devices to be turned on or off. Analog outputs, on the other hand, provide continuous control signals that can vary within a specific range, allowing for precise control over devices like variable frequency drives (VFDs) for motor speed control.
Actuator Control: Direct and Indirect PLC outputs control actuators in two primary ways: direct and indirect control. In direct control, the PLC output directly drives the actuator. For example, a digital output could turn on a motor or activate a solenoid.
In indirect control, the PLC output activates intermediate components such as relays or contactors. These components, in turn, control the power supply to the actuators. Indirect control is often used when the PLC’s output capacity is insufficient to directly handle the power requirements of the actuator.
Feedback Loops and Closed-Loop Control Many industrial processes require precise control and monitoring. In such cases, PLCs use feedback loops, where sensors provide feedback to the controller about the state or performance of the process. This allows the PLC to adjust its output signals in real-time to maintain desired conditions. For example, a temperature control system might use a temperature sensor’s feedback to adjust the heating element’s power via a proportional-integral-derivative (PID) algorithm.
Safety and Redundancy in Outputs Safety is a critical aspect of industrial automation. PLC outputs often include redundant systems to ensure reliable operation. Safety relays and interlock systems ensure that dangerous conditions are avoided, even in the event of a component failure.
Sequencing and Logic Control PLCs also excel at sequencing and logic control. They can execute complex sequences of actions by coordinating outputs in response to specific conditions. This is especially valuable in applications such as assembly lines, where precise timing and synchronization are essential.
Human-Machine Interface (HMI) Integration Modern PLC systems often integrate with Human-Machine Interfaces (HMIs) to provide operators with a visual representation of the automation process. Operators can monitor and control the system through the HMI, and the HMI can send commands to the PLC outputs.
In conclusion, PLC outputs are the backbone of actuation control in industrial automation. They enable the translation of digital decisions into physical actions by commanding actuators to perform specific tasks. With the ability to provide precise and timely control, PLCs play a pivotal role in enhancing the efficiency, safety, and reliability of various industrial processes.
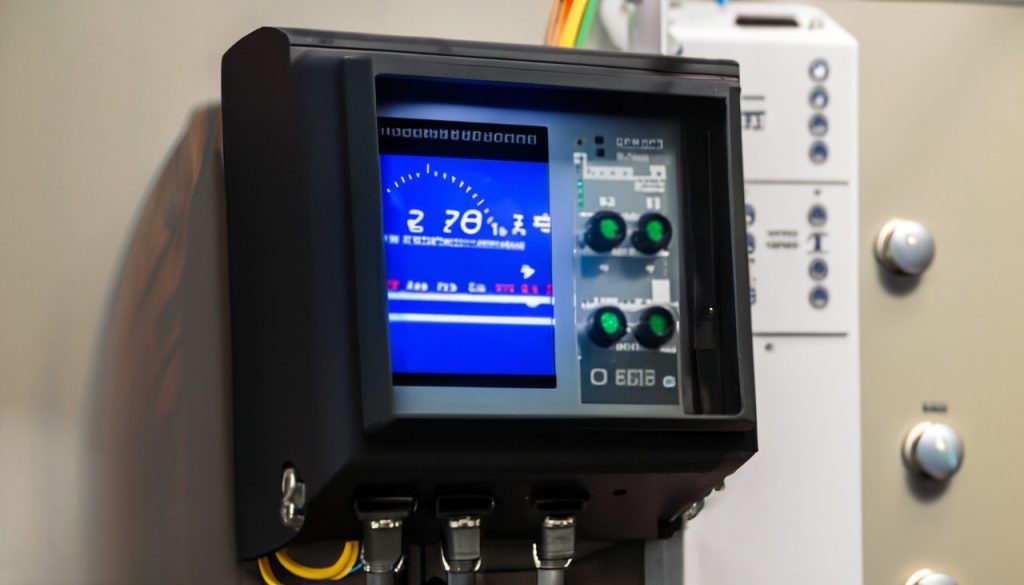
Programming Logic for Sensor-Actuator Interfacing
Programming the logic for sensor-actuator interfacing is a fundamental aspect of industrial automation that enables the coordination between sensors, Programmable Logic Controllers (PLCs), and actuators. This logic dictates how the PLC interprets input data from sensors and generates output signals to control actuators, thereby orchestrating the desired automation processes. Here, we delve into the key concepts and steps involved in programming this logic.
1. Sensor Input Acquisition: The first step in programming sensor-actuator interfacing is to acquire data from the sensors. This involves reading the analog or digital signals produced by the sensors. The programming code should include instructions to interface with the appropriate input modules on the PLC to retrieve sensor data accurately.
2. Signal Processing and Conditioning: Raw sensor data often requires processing and conditioning before it can be used effectively. For analog signals, this may involve scaling, converting, and filtering the data to match the physical parameter being measured. Digital signals may need debouncing to eliminate noise-induced fluctuations. Implementing these processing steps ensures accurate and reliable input data for decision-making.
3. Logic and Decision-Making: Programming logic involves creating decision-making algorithms that use the processed sensor data to determine the appropriate control actions. For instance, if a temperature sensor’s reading exceeds a certain threshold, the logic might dictate turning on a cooling system or sending an alert to the operator.
4. Control Algorithms: Control algorithms define how the actuators should respond based on sensor data. These algorithms can range from simple on/off control to more complex proportional-integral-derivative (PID) control for maintaining specific conditions such as temperature, pressure, or position.
5. Feedback Loops: Implementing feedback loops is essential for closed-loop control. The PLC continually monitors the output of the actuators and compares it with the desired state based on sensor data. If there’s a discrepancy, the PLC adjusts the control signals to bring the system back to the desired condition.
6. Output Generation and Actuator Control: After processing input data and determining the appropriate control actions, the PLC generates output signals to control the actuators. These outputs can trigger the activation, deactivation, or modulation of actuators like motors, solenoids, or valves.
7. Safety and Error Handling: Programming logic should incorporate safety features and error-handling mechanisms. For example, if a critical sensor fails or indicates hazardous conditions, the logic should implement emergency shutdown procedures to prevent accidents.
8. Human-Machine Interface (HMI) Integration: Incorporating an HMI allows operators to interact with the system and monitor its status. The programming logic should facilitate the exchange of information between the HMI and the PLC. Operators can use the HMI to change setpoints, view alarms, and manually control actuators if needed.
9. Testing and Validation: Programming logic should undergo thorough testing and validation before deployment. Simulation tools and test environments can be used to ensure that the logic behaves as intended and that the system responds correctly to different scenarios.
10. Maintenance and Adaptation: Industrial processes evolve over time, and the programming logic should be adaptable. Regular maintenance might involve updating setpoints, modifying control algorithms, or integrating new sensors and actuators. The programming should be designed to accommodate these changes without disrupting the overall system.
Programming logic for sensor-actuator interfacing is the backbone of industrial automation. By translating sensor data into control actions for actuators, this logic enables efficient, precise, and reliable management of complex processes. Careful consideration of processing steps, decision-making algorithms, and safety measures is essential to creating effective programming logic that enhances productivity and safety in industrial environments.
Communication Protocols and Networks
In the realm of industrial automation, effective communication is essential for coordinating complex processes, exchanging data, and controlling machinery. Communication protocols and networks play a pivotal role in ensuring seamless and reliable data exchange between various components, including sensors, Programmable Logic Controllers (PLCs), Human-Machine Interfaces (HMIs), and other devices. Here, we explore the significance of communication protocols and networks in industrial automation.
Communication Protocols: Building Common Language Communication protocols are sets of rules and conventions that devices follow to exchange data. They establish a common language that devices use to understand and interpret information correctly. In industrial automation, different devices often use different protocols, making it crucial to choose appropriate protocols for effective communication.
Common Industrial Communication Protocols:
- Modbus: A widely used serial communication protocol for connecting PLCs, sensors, and other devices. It supports both ASCII and binary representations and is known for its simplicity and versatility.
- Profibus: A popular fieldbus protocol used for communication between industrial automation devices. It supports high-speed data exchange and is suitable for complex systems.
- Ethernet/IP: An industrial Ethernet protocol that combines standard Ethernet communication with industrial automation capabilities. It’s often used for real-time control and high-speed data exchange.
- CAN (Controller Area Network): A protocol commonly used in automotive and manufacturing industries for connecting sensors, actuators, and other devices in a network.
- Profinet: Another industrial Ethernet protocol that offers high-speed communication and supports real-time data exchange, making it suitable for demanding automation tasks.
Benefits of Communication Protocols:
- Efficiency: Communication protocols ensure efficient data exchange by minimizing data overhead and optimizing transmission speeds.
- Interoperability: Devices from different manufacturers can communicate effectively if they follow the same protocol standards.
- Reliability: Robust protocols are designed to handle noise, interference, and communication errors often present in industrial environments.
- Flexibility: Different protocols offer varying levels of data integrity, speed, and real-time capabilities, allowing them to be chosen based on specific application requirements.
Communication Networks: Infrastructure for Connectivity Communication networks provide the physical infrastructure through which devices communicate. They connect sensors, PLCs, HMIs, and other components, creating a cohesive system that enables data exchange and control.
Types of Communication Networks:
- Fieldbus Networks: Used for communication between devices within a localized area. Examples include Profibus, DeviceNet, and AS-Interface.
- Industrial Ethernet Networks: Utilize standard Ethernet technology for high-speed communication over larger distances. Examples include Ethernet/IP, Profinet, and EtherCAT.
- Wireless Networks: Enable communication without physical cables. They’re useful in situations where wired connections are impractical or in areas with mobility requirements.
- Internet of Things (IoT) Networks: Enable devices to communicate over the internet, allowing remote monitoring and control of industrial processes.
Benefits of Communication Networks:
- Scalability: Networks can be designed to accommodate various numbers of devices, from small-scale systems to large, complex setups.
- Flexibility: Different types of networks can coexist within a single system, allowing devices to communicate optimally according to their requirements.
- Remote Monitoring and Control: Networks facilitate remote access to data and control, enabling efficient management and troubleshooting.
- Real-Time Capabilities: Some networks are designed to offer real-time communication, which is essential for time-sensitive processes and applications.
Communication protocols and networks are the lifelines of industrial automation. They ensure that devices can communicate effectively, leading to enhanced efficiency, reliability, and control in various industries. Selecting the right protocols and network infrastructure is crucial for building automation systems that meet the specific demands of modern industrial processes.
Conclusion
In the world of industrial automation, the seamless integration of Programmable Logic Controllers (PLCs) with sensors and actuators forms the bedrock of efficient and precise control systems. This synergy between digital intelligence and physical execution drives modern manufacturing processes, enhances productivity, ensures safety, and optimizes resource utilization.
Sensors serve as the eyes and ears of automation systems, collecting real-time data from the physical world and providing critical insights into the state of processes and equipment. Actuators, on the other hand, translate digital instructions into tangible actions, enabling the manipulation of machinery and systems. The interfacing of PLCs with sensors and actuators bridges the gap between these two worlds, allowing for real-time decision-making and control.
Communication protocols and networks facilitate this interaction, enabling devices to exchange data and collaborate seamlessly. Different types of sensors and actuators, each with their unique characteristics, demands, and interfaces, require careful consideration during the design phase. The programming logic that governs these interactions determines how sensors’ inputs are processed, decisions are made, and actuators’ outputs are controlled. This logic encapsulates the essence of automation, orchestrating processes with precision, intelligence, and adaptability.
As industries continue to embrace automation for enhanced efficiency and competitiveness, the integration of PLCs with sensors and actuators becomes increasingly sophisticated. The harmonious collaboration between these components empowers industries to achieve consistent quality, reduce human intervention, respond swiftly to changes, and even predict potential issues through advanced data analysis. Moreover, it creates a foundation for scalable and adaptable automation systems that can accommodate evolving technologies and business needs.
Interfacing of PLCs with sensors and actuators symbolizes the fusion of innovation, engineering, and industrial needs. This convergence not only transforms manufacturing landscapes but also shapes the future of technology-driven industrial processes. By establishing a bridge between the digital and physical realms, this integration propels industries towards greater efficiency, accuracy, and progress in the realm of industrial automation.