In the realm of modern industrial automation and control systems, Programmable Logic Controllers (PLCs) stand as the silent architects of precision, efficiency, and reliability. Born out of the necessity to streamline and automate industrial processes, PLCs have revolutionized manufacturing, production, and various industrial operations across diverse sectors.
A Programmable Logic Controller, at its core, is a digital computing device meticulously designed to execute specific tasks within industrial environments. What sets PLCs apart from general-purpose computers is their specialization in real-time control of machinery and processes. Initially introduced as a replacement for hardwired relay systems, PLCs have evolved into sophisticated instruments capable of overseeing complex operations with minimal human intervention.
The fundamental essence of a PLC lies in its programmability. Engineers and automation experts can develop tailored programs using specialized programming languages, often resembling ladder logic diagrams, to orchestrate the behavior of connected devices. This adaptability empowers industries to swiftly adapt to changing production requirements, implement intricate sequencing, and enhance safety measures.
Over the years, PLCs have transcended their original role and become integral to the implementation of Industry 4.0 principles. They now collaborate seamlessly with sensors, actuators, Human-Machine Interfaces (HMIs), and even cloud-based systems, ushering in an era of interconnectedness and data-driven decision-making.
This exploration will delve deeper into the inner workings of PLCs, their historical evolution, the principles that underpin their functionality, and the transformative impact they continue to exert on industries worldwide. From automotive manufacturing to pharmaceuticals, from energy distribution to food processing, PLCs remain the steadfast guardians of precision, automation, and operational excellence.
Components of a PLC System
A Programmable Logic Controller (PLC) system is a sophisticated arrangement of interconnected components designed to facilitate the automation, control, and monitoring of industrial processes. Each component plays a vital role in the overall functionality of the system, ensuring smooth operations and efficient management. Let’s explore the key components of a PLC system:
- Central Processing Unit (CPU): The CPU is the brain of the PLC system, responsible for executing the control program, managing data processing, and coordinating communication between various components. It interprets the user-programmed logic and supervises the overall operation of the system.
- Memory: PLCs have two primary types of memory: program memory (where the user’s control logic is stored) and data memory (for temporary data storage during program execution). Program memory retains the logic developed by engineers using programming languages, while data memory stores values, statuses, and intermediate results.
- Input Modules: Input modules serve as the sensory organs of the PLC system. They receive signals from sensors, switches, and other input devices that monitor the state of the controlled process. These signals are then converted into digital data that the PLC can process.
- Output Modules: Output modules act as the actuators of the system, translating digital signals from the CPU into physical actions. These actions can include controlling motors, valves, solenoids, and other devices that affect the process being controlled.
- Power Supply: A stable and reliable power supply is crucial for the proper functioning of a PLC system. It ensures that the components receive the necessary voltage levels to operate efficiently and without interruption.
- Communication Ports: PLCs often feature communication ports that facilitate data exchange between the PLC and external devices or systems. This can include Human-Machine Interfaces (HMIs), supervisory systems, remote monitoring devices, or even integration with higher-level networks.
- Programming Device: Engineers use programming devices, such as computers or specialized programming panels, to create and modify the logic that governs the PLC’s behavior. Programming can be done using various languages, including ladder logic, function block diagrams, structured text, and more.
- Rack/Chassis: The rack or chassis provides a physical framework for housing the various modules of the PLC system. It also offers a structure for proper wiring, organization, and cooling of the components.
- I/O (Input/Output) Bus: The I/O bus acts as a communication highway that connects the input and output modules to the CPU. It allows the exchange of data between the CPU and external devices quickly and efficiently.
- Special Function Modules: Depending on the complexity of the controlled process, specialized modules might be added to the system. These modules can provide functions like high-speed counting, analog signal processing, temperature measurement, and communication with specific industrial protocols.
- Backup and Redundancy Modules: To ensure system reliability and minimize downtime, some PLC systems incorporate backup or redundant components. These components can take over in case of a failure, enhancing system resilience.
The synergy between these components forms the foundation of a PLC system, enabling precise control, automation, and monitoring of industrial processes. As technology advances, PLC systems continue to evolve, integrating seamlessly with other technologies to enhance efficiency, connectivity, and overall performance.
PLC Operation Cycle
The operation cycle of a Programmable Logic Controller (PLC) outlines the sequence of events that occur within the controller’s processing loop to execute a control program. This cycle, often referred to as the “scan cycle” or “execution cycle,” is a continuous and repetitive process that enables the PLC to monitor inputs, execute programmed logic, and update outputs. The following steps provide an overview of the PLC operation cycle:
- Input Scan:
- The cycle begins with an input scan, where the PLC reads the current state of input devices such as sensors, switches, and other external signals.
- Each input module is sequentially checked to determine the status of its associated input devices.
- The PLC records the state of each input as either ON or OFF, based on the received signals.
- Program Execution:
- Once the input scan is complete, the PLC enters the program execution phase.
- The control program, developed by engineers using programming languages like ladder logic or structured text, is executed by the CPU.
- The program’s logic is processed to make decisions and perform calculations based on the input statuses.
- Instructions within the program can include conditional statements, loops, timers, and other control functions.
- Output Update:
- After the program execution phase, the PLC updates the output devices based on the results of the program’s logic.
- Output modules associated with specific output devices, such as motors, valves, and indicators, are activated or deactivated according to the control program’s instructions.
- Output Scan:
- Following the output update, the PLC enters the output scan phase.
- The PLC reviews the state of the output devices to ensure they reflect the desired output statuses as dictated by the executed control program.
- Communication and Housekeeping:
- In this phase, the PLC can engage in communication with external devices, such as Human-Machine Interfaces (HMIs), supervisory systems, or other PLCs within a network.
- Data exchange, remote monitoring, and system diagnostics can occur during this phase.
- Housekeeping tasks, such as managing memory and maintaining system integrity, may also be performed.
- Cycle Completion and Repeat:
- With the completion of the communication and housekeeping phase, the PLC cycle concludes.
- The cycle then repeats itself at a predefined scan rate, which determines how often the PLC goes through these steps.
- The entire operation cycle typically occurs within milliseconds or microseconds, allowing for real-time control of processes.
It’s important to note that during each PLC operation cycle, the program execution phase is the most crucial and resource-intensive. Engineers must design efficient and optimized control logic to ensure the program can run within the scan time and meet the required control performance. Additionally, some PLCs may offer advanced features like interrupt routines, which allow certain critical tasks to interrupt the regular scan cycle for immediate execution.
Understanding the PLC operation cycle is fundamental to creating reliable and responsive control systems, enabling industries to automate and manage complex processes with precision and efficiency.
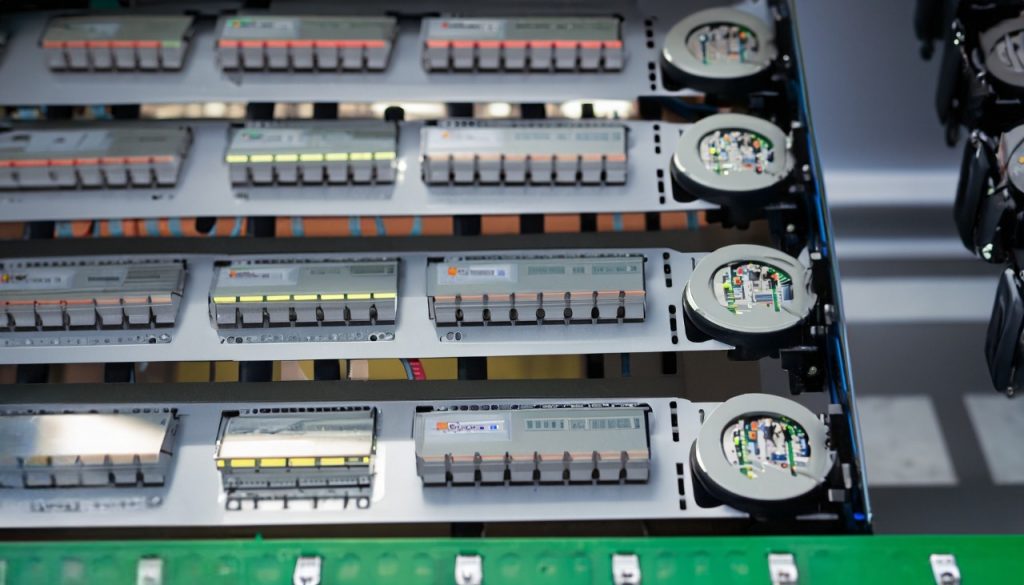
PLC Applications
Programmable Logic Controllers (PLCs) find application across a diverse range of industries and sectors, providing a powerful platform for automation, control, and monitoring. Their flexibility, reliability, and ability to withstand harsh industrial environments make them invaluable tools in optimizing processes, increasing efficiency, and enhancing safety. Here are some notable PLC applications:
- Manufacturing and Production: PLCs are widely used in manufacturing plants to automate assembly lines, control machinery, and manage production processes. They can handle tasks such as material handling, robotic control, packaging, quality control, and more. PLCs enable consistent and precise manufacturing operations, leading to increased productivity and reduced defects.
- Automotive Industry: In automotive manufacturing, PLCs control assembly lines, welding robots, paint booths, and conveyor systems. They ensure synchronized operations, error detection, and quality control, contributing to the efficient production of vehicles.
- Food and Beverage Industry: PLCs play a vital role in food processing, packaging, and bottling operations. They regulate cooking, mixing, temperature control, filling, and labeling processes, ensuring compliance with hygiene standards and maintaining product consistency.
- Energy Management: PLCs are used in power generation, distribution, and management. They control turbine generators, monitor energy consumption, manage substations, and optimize energy efficiency through load shedding and demand management strategies.
- Water Treatment and Utilities: PLCs are integral to wastewater treatment plants, controlling pumps, valves, chemical dosing, and filtration systems. They monitor water quality, manage distribution networks, and ensure compliance with environmental regulations.
- Oil and Gas Industry: PLCs are employed in oil refineries, petrochemical plants, and drilling operations. They manage critical processes such as wellhead control, pipeline monitoring, and safety shutdown systems.
- Pharmaceutical Industry: In pharmaceutical manufacturing, PLCs control complex processes like drug formulation, blending, tablet compression, and sterilization. They maintain precise conditions to ensure product quality and regulatory compliance.
- Building Automation: PLCs are used in building management systems to control lighting, HVAC (heating, ventilation, and air conditioning), security systems, access control, and fire detection. They enhance occupant comfort, safety, and energy efficiency.
- Material Handling and Logistics: PLCs automate warehouse operations, conveyor systems, sorting mechanisms, and automated guided vehicles (AGVs). They optimize material flow, reduce errors, and increase throughput.
- Mining and Metals Industry: PLCs control conveyor belts, crushers, smelting furnaces, and material handling equipment in mining and metals operations. They improve safety by enabling remote control of hazardous processes.
- Packaging Industry: PLCs govern packaging machines, ensuring accurate filling, sealing, labeling, and quality control. They enhance packaging consistency and reduce waste.
- Agriculture: PLCs are used in precision agriculture for automated irrigation, monitoring of soil conditions, and control of agricultural machinery.
These examples showcase the versatility of PLCs in various industries, where their ability to automate tasks, enhance process control, and gather real-time data proves instrumental in achieving operational excellence, cost savings, and improved product quality. As technology continues to advance, PLCs will undoubtedly find even more innovative applications, shaping the future of industrial automation.
Future Trends in PLCs
The realm of Programmable Logic Controllers (PLCs) is evolving rapidly, driven by technological advancements and changing industry demands. As we look toward the future, several trends are shaping the evolution of PLCs and their role in industrial automation:
- Industry 4.0 Integration: PLCs are becoming a crucial component of the Industry 4.0 paradigm, where the convergence of digital, physical, and cyber-physical systems leads to highly interconnected and intelligent manufacturing environments. PLCs are expected to seamlessly integrate with Industrial Internet of Things (IIoT) devices, cloud computing, big data analytics, and artificial intelligence (AI) systems to create smart factories that enable predictive maintenance, remote monitoring, and real-time data-driven decision-making.
- Edge Computing and Edge PLCs: Edge computing involves processing data closer to the source rather than sending it to a centralized cloud server. Edge PLCs, designed for edge computing, will enable faster response times and reduced network congestion by processing critical control and monitoring tasks directly at the machine level. This approach enhances system resilience and reduces reliance on constant cloud connectivity.
- Cybersecurity Enhancements: With increased connectivity, the importance of cybersecurity in industrial automation has grown significantly. Future PLCs will include advanced security features to protect against cyber threats and unauthorized access. Secure communication protocols, encryption, authentication mechanisms, and intrusion detection systems will be integrated into PLC designs.
- AI and Machine Learning Integration: PLCs will incorporate AI and machine learning capabilities to analyze complex data patterns and make intelligent decisions. This will enable predictive maintenance, anomaly detection, optimization of control parameters, and improved process efficiency.
- Virtualization and Simulation: Virtual PLCs and simulation tools will become more prevalent for testing and optimizing control programs before implementation. This reduces downtime and enhances system reliability by minimizing potential errors.
- Enhanced Diagnostics and Condition Monitoring: Future PLCs will provide more sophisticated diagnostic tools, enabling operators to monitor the health and performance of machinery and processes in real-time. Predictive maintenance algorithms will identify issues before they lead to failures.
- Open Source and Standardization: Open-source PLC platforms and standardized programming languages will gain traction, making it easier for engineers and developers to create and share control programs across different devices and manufacturers.
- Energy Efficiency and Sustainability: PLCs will continue to play a significant role in optimizing energy consumption and reducing environmental impact. They will control systems that automatically adjust energy usage based on real-time demand, contributing to sustainability efforts.
- 5G Connectivity: The rollout of 5G networks will enable faster and more reliable communication between PLCs and external systems. This will support real-time monitoring and control in applications that require extremely low latency.
- Human-Centric Interfaces: PLCs will incorporate more intuitive Human-Machine Interfaces (HMIs) with features like augmented reality (AR) and virtual reality (VR) for enhanced operator interaction and troubleshooting.
These future trends highlight the transformative potential of PLCs in reshaping industrial automation and control systems. As PLC technology continues to evolve, industries will benefit from increased efficiency, productivity, safety, and adaptability to changing market demands.
Conclusion
Gaining an understanding of the basics of Programmable Logic Controllers (PLCs) provides a fundamental insight into the heart of modern industrial automation. These versatile devices have revolutionized the way industries operate by offering a dynamic and adaptable approach to controlling processes and machinery. With their ability to process input data, execute programmed logic, and produce precise output actions, PLCs have become the backbone of countless sectors, ranging from manufacturing and energy to agriculture and logistics.
The components of a PLC system, including the CPU, memory, input and output modules, communication ports, and programming devices, come together in a harmonious symphony to orchestrate intricate industrial operations. This technology has evolved from its origins as a replacement for hardwired relay systems into a sophisticated platform capable of integrating with advanced technologies like the Industrial Internet of Things (IIoT), artificial intelligence (AI), and edge computing.
As industries continue to embrace innovation, PLCs are poised to play an even more pivotal role in shaping the future of automation. With trends such as Industry 4.0 integration, AI infusion, enhanced cybersecurity, and energy efficiency optimization, PLCs are poised to transform factories and facilities into interconnected, intelligent, and efficient environments.
Mastering the basics of PLCs not only empowers engineers, technicians, and operators with the knowledge to design, implement, and maintain control systems effectively, but also equips them to stay at the forefront of technological advancements in the ever-evolving landscape of industrial automation. From manufacturing processes that demand precision to complex systems requiring real-time decision-making, PLCs remain the cornerstone of progress, enabling industries to achieve greater efficiency, safety, and sustainability in a dynamic and interconnected world.