Controllers play a pivotal role in various fields, from engineering and technology to automation and even in our day-to-day lives. They are devices or systems designed to regulate, manage, and maintain desired conditions or behaviors of a given system. The primary purpose of a controller is to ensure that a system behaves in a certain way or achieves specific objectives, despite external disturbances or variations.
In engineering and automation, controllers are integral components of systems that require precision, stability, and adaptability. They are commonly used in industries such as manufacturing, aerospace, automotive, and robotics to maintain consistent and accurate performance of machines and processes. By continuously monitoring the system’s state and making real-time adjustments, controllers enhance efficiency, productivity, and safety.
The fundamental principle behind controllers is feedback control. This involves sensing the current state or output of a system, comparing it to a desired or reference state, and then using this error information to adjust the system’s input or parameters. The feedback loop allows controllers to maintain the system’s behavior within desired limits, even when there are disturbances or changes in operating conditions.
Importance of Controllers
Controllers are central to the functioning of various systems, industries, and technologies, playing a crucial role in achieving stability, accuracy, efficiency, and desired outcomes. Their significance extends across numerous domains, ranging from industrial processes and manufacturing to transportation, robotics, and everyday devices. Here are some key reasons highlighting the importance of controllers:
- Automation and Precision: Controllers automate processes by continuously monitoring system conditions and making adjustments in real time. This level of automation leads to increased precision, as controllers can fine-tune parameters to maintain optimal performance. In manufacturing, for instance, controllers regulate production lines to ensure consistent product quality.
- Stability and Safety: Controllers contribute to system stability by mitigating the effects of disturbances and uncertainties. They help maintain safe operating conditions by preventing overshooting, oscillations, or catastrophic failures. In critical systems such as nuclear reactors or aircraft, controllers are essential for preventing dangerous situations.
- Energy Efficiency: Energy consumption is a significant concern in many applications. Controllers optimize energy usage by adjusting parameters in response to varying conditions. Heating, ventilation, and air conditioning (HVAC) systems, as well as smart lighting, benefit from controllers that minimize energy wastage.
- Reduced Human Intervention: Controllers reduce the need for constant human intervention, freeing up resources and enabling personnel to focus on more complex tasks. For instance, autonomous vehicles utilize controllers to navigate and respond to changing traffic conditions.
- Consistency and Reproducibility: In manufacturing and industrial processes, controllers ensure consistent output and reproducibility. This is crucial for meeting quality standards and customer expectations, as variations can be minimized through precise control.
- Adaptability to Changing Conditions: Many systems operate in environments with changing conditions. Controllers can adapt to these variations, whether it’s adjusting the flight path of a drone in windy conditions or regulating the temperature of a greenhouse as weather patterns change.
- Enhanced Performance: Controllers optimize system performance by adjusting parameters in real time based on feedback. This leads to improved response times, reduced errors, and optimized throughput in various applications.
- Complex System Management: Modern technologies often involve complex systems with interconnected components. Controllers manage these complexities by coordinating actions and maintaining harmony among subsystems. This is particularly evident in smart grids, where controllers balance electricity demand and supply.
- Real-Time Decision Making: Controllers enable real-time decision making by processing data and generating control signals rapidly. This capability is vital in applications like medical devices, where split-second decisions can have life-saving implications.
- Scientific Research and Exploration: Controllers are essential in scientific research and exploration. In space missions, for example, controllers guide spacecraft through intricate maneuvers, ensuring precise data collection and successful mission outcomes.
- Innovation and Advancements: The development of new controllers and control strategies drives innovation. As technology evolves, more sophisticated controllers emerge, enabling the creation of novel products, systems, and solutions.
In essence, controllers serve as the bridge between desired objectives and actual system behavior. They allow us to harness the benefits of automation, optimization, and efficient resource utilization across a wide spectrum of applications. The importance of controllers cannot be overstated, as they contribute to the reliability, safety, and progress of numerous industries and technologies.
Basic Components of Controllers
Controllers are intricate systems designed to regulate, manage, and control the behavior of various processes and devices. They consist of several fundamental components that work in tandem to ensure that a system operates according to desired specifications. These components vary based on the type of controller and its intended application, but here are the core components commonly found in most controllers:
- Sensors: Sensors are the “eyes” and “ears” of a controller. They gather data about the current state of the system or process being controlled. This data can include measurements like temperature, pressure, position, velocity, and more. Sensors convert physical or environmental quantities into electrical signals that the controller can interpret and use for decision-making.
- Actuators: Actuators are the “muscles” of a controller. They receive control signals from the controller and initiate physical changes in the system. Actuators can take various forms, such as motors, valves, solenoids, and relays. They exert control over processes by adjusting parameters like speed, position, flow, and more.
- Controller Algorithm: The controller algorithm is the heart of the control system. It is a set of mathematical equations, logic rules, or algorithms that process the data from sensors and generate control signals for the actuators. The algorithm’s purpose is to calculate the appropriate corrective action to bring the system’s behavior closer to the desired state.
- Reference Signal: The reference signal, also known as the setpoint or desired value, represents the target state that the system should achieve. The controller compares the reference signal with the actual system output (sensed by sensors) to determine the error, which guides the control actions.
- Feedback Loop: The feedback loop is the mechanism that closes the control loop. It involves continuously comparing the actual system output (measured by sensors) with the reference signal. The resulting error signal is then processed by the controller algorithm to adjust the control signal sent to the actuators. The feedback loop ensures that the system’s behavior remains within desired limits and compensates for disturbances.
- Control Signal: The control signal is the output of the controller algorithm. It is a signal sent to the actuators to influence the system’s behavior. The control signal might dictate the speed of a motor, the opening of a valve, or any other relevant action that alters the system’s state.
- Processor and Computing Unit: The processor or computing unit executes the controller algorithm. It processes the sensor data, calculates the control signal, and manages the overall control logic. In modern controllers, this component can range from simple microcontrollers to powerful computing platforms, depending on the complexity of the application.
- Interfaces and User Inputs: Many controllers have user interfaces that allow operators to interact with the system. These interfaces can include buttons, knobs, touch screens, or digital interfaces for configuring settings, adjusting parameters, and monitoring system status.
- Communication Interfaces: In interconnected systems, controllers often need to communicate with other devices or systems. Communication interfaces enable controllers to exchange data, commands, and information with external components, such as other controllers, computers, or remote monitoring systems.
These components collectively enable controllers to regulate processes, maintain stability, and achieve desired outcomes. The synergy between sensors, actuators, algorithms, and feedback mechanisms empowers controllers to operate autonomously, making them indispensable tools in fields as diverse as manufacturing, aerospace, automotive, healthcare, and beyond.
Types of Controllers
- Proportional-Integral-Derivative (PID) Controllers: PID controllers are among the most widely used controllers in industrial processes. They calculate control actions based on proportional, integral, and derivative terms. The proportional term responds to the current error, the integral term considers the accumulation of past errors, and the derivative term anticipates future error trends. PID controllers provide a balance between responsiveness, stability, and steady-state accuracy.
- On-Off (Bang-Bang) Controllers: On-Off controllers are simple but effective. They switch between fully on and fully off states based on the error between the desired setpoint and the current process value. When the error crosses a predefined threshold, the controller switches states. While easy to implement, on-off controllers can lead to frequent switching near the setpoint, causing oscillations and inefficiencies.
- Proportional Controllers: Proportional controllers adjust the control signal based solely on the proportional error between the setpoint and the actual process value. They provide a control signal proportional to the error, which helps reduce overshooting compared to on-off controllers. However, they might not eliminate steady-state error completely.
- Integral Controllers: Integral controllers focus on eliminating steady-state error by considering the accumulated integral of past errors. They continuously adjust the control signal based on the integral of the error, making them effective at eliminating any long-term deviations from the setpoint.
- Derivative Controllers: Derivative controllers anticipate the future trend of the error and adjust the control signal accordingly. They provide a control signal proportional to the rate of change of the error. Derivative action helps dampen overshoot and improve stability in systems with fast changes.
- Fuzzy Logic Controllers: Fuzzy logic controllers use linguistic variables and fuzzy sets to handle imprecise or uncertain information. These controllers are particularly useful when the relationship between inputs and outputs is complex or when human-like decision-making processes are involved. They excel in systems that require expert knowledge to make control decisions.
- Adaptive Controllers: Adaptive controllers adjust their parameters in real-time based on the changing characteristics of the system they’re controlling. They are particularly useful when system dynamics are uncertain or change over time. Adaptive controllers ensure that the control strategy remains effective even as conditions evolve.
- Model Predictive Controllers: Model Predictive Controllers (MPC) utilize predictive models of the system to optimize future control actions. These controllers predict the system’s behavior over a certain time horizon and then compute control signals that optimize a predefined cost function. MPC is often used in advanced industrial processes and autonomous systems.
- Nonlinear Controllers: Nonlinear controllers are designed to handle systems with nonlinear behaviors. Unlike linear controllers, which assume linear relationships between inputs and outputs, nonlinear controllers account for more complex dynamics, making them suitable for a wide range of applications.
- Digital Controllers: Digital controllers process data in discrete time steps, making them suitable for digital systems and microcontroller-based applications. They convert continuous signals from sensors into digital format and implement control algorithms using computational logic.
These are just a few examples of the many types of controllers available, each with its own strengths and limitations. The choice of controller type depends on the specific application, the nature of the system being controlled, and the desired performance criteria.
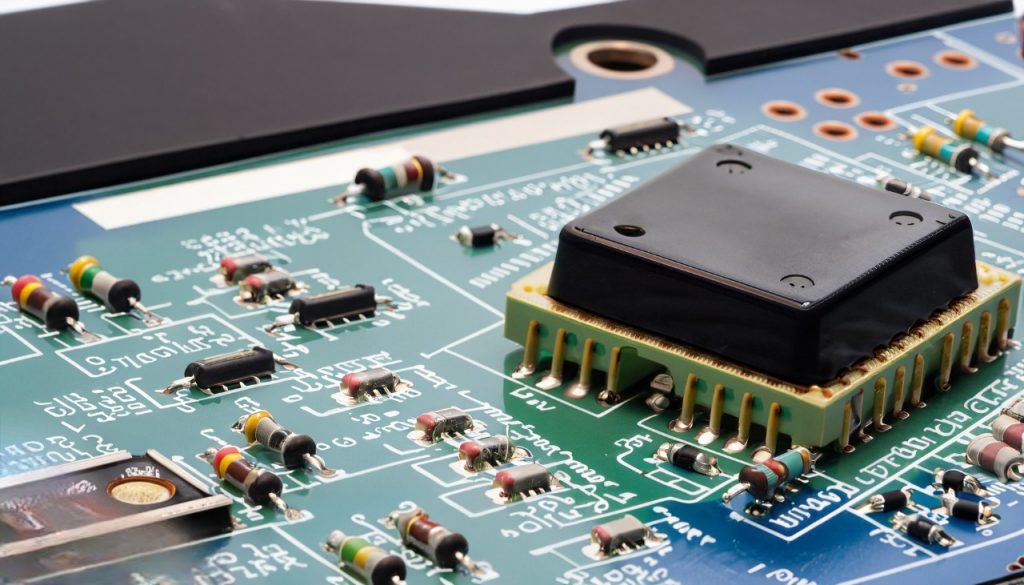
Controller Design and Tuning
Controller design and tuning are critical processes in ensuring that a control system functions optimally, meeting desired performance criteria and stability requirements. The goal of these processes is to determine the appropriate controller type, parameters, and settings that allow the controlled system to respond accurately and efficiently to changes in its environment or setpoint. Let’s explore the key aspects of controller design and tuning:
1. Controller Design: Controller design involves selecting the type of controller that best suits the system’s dynamics and designing the control algorithm that generates the control signal. Here’s a general approach to controller design:
- System Modeling: Develop a mathematical model that represents the behavior of the system. This model helps understand how the system responds to different inputs and disturbances.
- Controller Type Selection: Choose a suitable controller type based on the system’s characteristics and requirements. For instance, a PID controller might work well for linear systems, while nonlinear systems may require more specialized controllers.
- Algorithm Development: Design the control algorithm that computes the control signal based on the error between the desired setpoint and the current system output. This algorithm often includes proportional, integral, and derivative terms, which are adjusted based on the system’s response.
- Feedback Loop Design: Establish the feedback loop by connecting sensors, actuators, and the controller. This loop ensures that the system continually adjusts its behavior to achieve the desired state.
2. Controller Tuning: Controller tuning involves adjusting the parameters of the controller to achieve desired performance while maintaining stability. Poorly tuned controllers can lead to overshooting, oscillations, slow responses, or even system instability. Here’s how to approach controller tuning:
- Stability Analysis: Before tuning, ensure the control system is stable. An unstable system will not respond predictably to control inputs and may lead to catastrophic failures.
- Performance Criteria: Define the desired performance criteria, such as settling time, overshoot, rise time, and steady-state error. Different applications may prioritize these criteria differently.
- Trial and Error: Start with initial guesses for the controller parameters and observe the system’s response. Adjust the parameters iteratively, analyzing how each change affects the system’s behavior.
- Analytical Methods: Some controller types, like PID controllers, have well-established tuning methods. Ziegler-Nichols, Cohen-Coon, and Tyreus-Luyben methods are examples of approaches to tune PID controllers analytically.
- Simulation: Utilize simulation software to model the system and test different tuning parameters virtually. Simulation helps avoid unnecessary adjustments on the real system and allows for rapid experimentation.
- Frequency Response Analysis: Analyze the system’s frequency response to understand how it behaves at different frequencies. This information can guide tuning decisions for advanced control strategies.
- Auto-Tuning: Many modern control systems offer auto-tuning features, where the controller adjusts its parameters automatically based on the system’s behavior. Auto-tuning reduces the manual effort required for optimization.
3. Iterative Process: Controller design and tuning are iterative processes. It’s rare to achieve perfect tuning on the first attempt. As the system operates and conditions change, periodic tuning adjustments might be necessary to maintain optimal performance.
In conclusion, controller design and tuning are essential for achieving effective control in various systems. A well-designed and properly tuned controller enhances stability, responsiveness, and efficiency, leading to improved overall system performance. It’s crucial to strike a balance between performance and stability and to consider the specific requirements of the application when designing and tuning controllers.
Advanced Controller Concepts
As technology continues to evolve, so does the field of control systems. Advanced controller concepts go beyond traditional control strategies to address complex and dynamic scenarios that require higher levels of sophistication, adaptability, and intelligence. These concepts leverage cutting-edge techniques and technologies to enhance control system performance and address challenging applications. Here are some advanced controller concepts:
1. Model Predictive Control (MPC): Model Predictive Control is a sophisticated approach that uses predictive models of the system to optimize control actions over a specified time horizon. MPC predicts the system’s behavior, factors in constraints, and computes control inputs that optimize a cost function. MPC is particularly useful for systems with constraints, multivariable interactions, and fast-changing dynamics, such as chemical processes and autonomous vehicles.
2. Adaptive Control: Adaptive control adjusts the controller’s parameters in real-time to accommodate changes in the system’s behavior or operating conditions. It’s particularly useful in systems with time-varying or uncertain dynamics. Adaptive controllers continually update their internal model of the system, allowing them to adapt to changes and maintain performance.
3. Neuro-Fuzzy Controllers: Neuro-Fuzzy controllers combine the strengths of fuzzy logic and neural networks. These controllers use fuzzy rules to handle linguistic information and neural networks to model complex, nonlinear relationships. They’re effective in systems with uncertain and nonlinear behavior, such as complex industrial processes.
4. Robust Control: Robust control focuses on designing controllers that perform well even when the system’s parameters vary or uncertainties are present. It accounts for worst-case scenarios and aims to provide stable and acceptable performance regardless of variations or disturbances. Robust control is crucial in safety-critical applications like aerospace and medical devices.
5. H-infinity Control: H-infinity control aims to minimize the impact of disturbances and uncertainties on the system’s performance. It designs controllers that maximize the system’s stability and performance while minimizing the sensitivity to external factors. H-infinity control is often used in applications where disturbance rejection is critical.
6. Nonlinear Control: Nonlinear control strategies address systems with complex and nonlinear behaviors. These controllers use advanced mathematical techniques to handle nonlinearity and ensure accurate control. Nonlinear control is relevant in fields like robotics, aerospace, and biotechnology.
7. Decentralized and Distributed Control: Decentralized and distributed control systems distribute control tasks across multiple agents or subsystems. Each agent makes decisions based on local information, contributing to a collective control objective. This concept is vital in large-scale systems, such as smart grids and industrial networks.
8. Optimal Control: Optimal control aims to find the control inputs that minimize a specified performance index while adhering to system constraints. This concept involves solving optimization problems to determine the best control actions. Optimal control is used in fields like economics, robotics, and autonomous systems.
9. Hybrid Control Systems: Hybrid control systems combine continuous dynamics with discrete-event logic. They address systems that involve both continuous processes and discrete decisions, like mechatronics systems and industrial automation.
10. Event-Triggered Control: Event-triggered control adjusts control actions only when specific events occur, minimizing the frequency of control updates. This approach reduces computational load and communication bandwidth in resource-constrained systems, such as wireless sensor networks.
Advanced controller concepts empower control systems to tackle complex challenges, adapt to changing conditions, and achieve higher levels of performance and efficiency. These concepts play a pivotal role in modernizing various industries and technologies, from manufacturing and robotics to energy management and beyond.
Conclusion
Controllers stand as the backbone of modern technology, offering a structured approach to maintaining, optimizing, and guiding the behavior of diverse systems. From the intricate machinery of industrial processes to the subtleties of household devices, controllers are the invisible hands that ensure precise outcomes and operational stability.
The diverse array of controller types, each equipped with its unique algorithms and strategies, highlights the adaptability and ingenuity of these systems. Whether through the proportional adjustments of PID controllers, the nuanced decision-making of fuzzy logic controllers, or the predictive capabilities of model-based approaches, controllers provide solutions tailored to the intricacies of each application.
Controllers facilitate automation, alleviate human intervention, and drive efficiency by harnessing real-time data from sensors, generating control signals for actuators, and maintaining a dynamic feedback loop. Their presence is integral in guaranteeing consistency, safety, and optimal performance, elevating industries such as manufacturing, transportation, energy management, and beyond.
As technology continues to advance, controllers will undoubtedly evolve, integrating advanced concepts like adaptive learning, artificial intelligence, and decentralized decision-making. This evolution will further shape how controllers enhance the efficiency, reliability, and precision of systems, underscoring their indispensable role in shaping our interconnected world. In a world marked by complexity and innovation, controllers remain a steadfast cornerstone, ensuring that the mechanisms of modern life operate seamlessly and with purpose.