A Programmable Logic Controller (PLC) is a specialized computer used in industrial automation and control systems to monitor and control various processes and machinery. PLCs utilize specific programming languages designed for creating logic and instructions that govern the behavior of industrial processes. These programming languages are tailored to the real-time nature of industrial automation, where precise and deterministic control is crucial.
There are several PLC programming languages, each with its own strengths and purposes. These languages allow engineers and programmers to define the behavior of a PLC in response to inputs, events, and conditions, ultimately controlling the outputs that drive actuators, motors, valves, and other industrial components.
Evolution of PLC Programming Languages
The evolution of PLC (Programmable Logic Controller) programming languages has been driven by the need for more efficient, flexible, and powerful ways to control industrial processes. Over the years, these languages have evolved to accommodate changing technological landscapes, industry demands, and the growing complexity of automation systems. Let’s explore the key stages in the evolution of PLC programming languages:
- Relay Ladder Logic:
- The earliest PLC programming languages were influenced by relay logic diagrams used in traditional control systems. The introduction of Ladder Logic (LD) in the late 1960s was a significant milestone. It provided an intuitive visual representation of control logic using symbols resembling electrical relay circuits. Ladder Logic was designed to bridge the gap between electrical engineers and programmers, making it easier to transition from relay-based control systems to PLCs.
- Textual Languages and Standardization:
- As industrial automation grew more complex, the need for more powerful programming languages emerged. In the 1980s, IEC 61131-3 was introduced as a standard to define a set of programming languages for PLCs. This standardization brought languages like Instruction List (IL), Structured Text (ST), and Sequential Function Chart (SFC) into play, catering to engineers with different programming backgrounds and allowing for more sophisticated control strategies.
- Modularity and Reusability:
- With the rise of modular design concepts, Function Block Diagram (FBD) was introduced as part of IEC 61131-3. FBD allowed programmers to create reusable function blocks, promoting modular programming and reducing duplication of code. This evolution improved code organization, maintenance, and overall system efficiency.
- Advanced Algorithms and Math:
- The demand for more advanced calculations and data processing capabilities led to the incorporation of high-level programming languages in PLCs. Structured Text (ST) gained popularity for its resemblance to traditional programming languages like Pascal and C. This language enabled engineers to implement complex algorithms, mathematical calculations, and data manipulations within PLC programs.
- Safety and Standard Compliance:
- Safety-critical industries necessitated the development of specialized languages and standards. IEC 61508 introduced safety programming languages and methodologies, such as Safety Function Block Diagrams (SFBD), to address safety-related control logic and ensure compliance with safety standards.
- Integration and Industry 4.0:
- The ongoing trend towards Industry 4.0 and the Industrial Internet of Things (IIoT) has prompted PLC programming languages to evolve further. Modern PLCs often support various communication protocols, allowing seamless integration with other devices and systems. Additionally, high-level languages and scripting capabilities enable PLCs to interact with databases, web services, and cloud platforms.
- Specialized Applications:
- Industries with unique requirements, such as robotics and motion control, have seen the emergence of specialized languages designed specifically for their needs. These languages enable precise control over robotic movements, trajectories, and interactions, enhancing automation capabilities in these fields.
- Graphical Programming and Visualization:
- The evolution of graphical programming environments, which combine traditional languages with intuitive visual representations, has further simplified PLC programming. These environments offer drag-and-drop functionality, allowing engineers to design control strategies by connecting pre-defined function blocks.
Evolution of PLC programming languages has been marked by a transition from simple relay logic to powerful, standardized languages capable of handling complex control strategies, safety requirements, and integration challenges. The ongoing convergence of automation and digitalization is likely to continue shaping the evolution of PLC programming languages, enabling even more sophisticated and connected industrial automation solutions.
Common PLC Programming Languages
PLC (Programmable Logic Controller) programming languages are crucial for creating control logic and instructions to automate industrial processes. Here are some of the common PLC programming languages that engineers and programmers use:
- Ladder Logic (LD): Ladder Logic is inspired by electrical relay logic diagrams. It uses graphical symbols to represent control logic visually, making it intuitive for electricians and technicians who are familiar with traditional control systems. Ladder Logic consists of rungs that contain contacts (representing inputs) and coils (representing outputs). These rungs are evaluated left to right, top to bottom, simulating the way electrical signals flow through relays.
- Function Block Diagram (FBD): FBD is a graphical programming language that represents control logic using interconnected function blocks. Each block performs a specific operation, and the connections between blocks indicate data flow and logic relationships. FBD is particularly useful for breaking down complex tasks into modular components, improving code reusability and maintenance.
- Structured Text (ST): Structured Text is a high-level textual programming language that resembles traditional programming languages like Pascal or C. It’s well-suited for complex calculations, mathematical operations, and data manipulation. ST allows programmers to write more sophisticated and efficient algorithms, making it a preferred choice for advanced control strategies.
- Instruction List (IL): Instruction List is a low-level textual programming language similar to assembly language. It uses mnemonic codes to represent individual instructions. While IL might be less human-readable, it’s beneficial when precise control over hardware is required or when performance optimization is a priority.
- Sequential Function Chart (SFC): SFC is used to model and control processes that follow a sequential order or specific states. It consists of steps, transitions, and actions. SFC visually represents the flow of a process, making it easier to understand and design complex sequences of operations.
- Structured Text (ST): ST is a high-level textual programming language that resembles traditional programming languages like Pascal. It’s well-suited for complex calculations, mathematical operations, and data manipulation. ST allows programmers to write more sophisticated and efficient algorithms, making it a preferred choice for advanced control strategies.
- Sequential Function Chart (SFC): SFC is used to model and control processes that follow a sequential order or specific states. It consists of steps, transitions, and actions. SFC visually represents the flow of a process, making it easier to understand and design complex sequences of operations.
- Graphical Function Blocks: Some PLC programming environments offer graphical function blocks, which allow programmers to create reusable blocks of logic with predefined functions. These blocks can be interconnected to build complex control strategies while maintaining modularity and ease of use.
- High-Level Languages: Some modern PLCs support high-level programming languages like C or C++. These languages provide extensive programming capabilities and are suitable for complex applications requiring advanced data processing and external communication.
- Structured Text (ST): ST is a high-level textual programming language that resembles traditional programming languages like Pascal. It’s well-suited for complex calculations, mathematical operations, and data manipulation. ST allows programmers to write more sophisticated and efficient algorithms, making it a preferred choice for advanced control strategies.
- Sequential Function Chart (SFC): SFC is used to model and control processes that follow a sequential order or specific states. It consists of steps, transitions, and actions. SFC visually represents the flow of a process, making it easier to understand and design complex sequences of operations.
- Graphical Function Blocks: Some PLC programming environments offer graphical function blocks, which allow programmers to create reusable blocks of logic with predefined functions. These blocks can be interconnected to build complex control strategies while maintaining modularity and ease of use.
- High-Level Languages: Some modern PLCs support high-level programming languages like C or C++. These languages provide extensive programming capabilities and are suitable for complex applications requiring advanced data processing and external communication.
Different industries and applications have varying requirements, and the choice of programming language depends on factors such as the complexity of the control strategy, the familiarity of the programmers, the need for reusability, and the performance demands of the system. Modern PLC programming environments often support multiple languages, enabling engineers to select the most suitable language for each aspect of the automation process.
Selection of Programming Language
The selection of a programming language for a PLC (Programmable Logic Controller) project is a crucial decision that can significantly impact the efficiency, reliability, and maintainability of the automation system. When choosing a programming language, several factors should be considered to ensure the best fit for the specific application and project requirements:
- Application Complexity: The complexity of the automation task plays a vital role in determining the appropriate programming language. For simple control tasks, such as basic logic operations, Ladder Logic might be sufficient. However, for more intricate processes involving calculations, data manipulation, and complex control strategies, a higher-level language like Structured Text could be more suitable.
- Programmer Familiarity: The expertise and familiarity of the programming team with different languages should be taken into account. If the team is experienced in a specific language, it might be more efficient to use that language to develop the PLC program.
- Modularity and Reusability: Some programming languages, like Function Block Diagram (FBD), promote modularity and code reusability. If the project involves creating reusable components or has a modular design, FBD or graphical function blocks could simplify development and maintenance.
- Performance Requirements: Applications with strict timing constraints or high-speed processes may benefit from languages that provide fine-grained control over execution timing, such as Instruction List (IL) or even low-level languages. These languages offer more direct control over the hardware and can optimize execution speed.
- Maintenance and Debugging: The ease of debugging and maintaining the code is a critical consideration. Graphical languages like Ladder Logic and Function Block Diagram offer visual representations that can help diagnose issues quickly. On the other hand, high-level languages like Structured Text can simplify debugging with clear error messages and advanced programming constructs.
- Data Processing: If the project involves extensive data manipulation, mathematical calculations, or data communication, a high-level language like Structured Text might provide the necessary capabilities for efficient data processing.
- Integration: Consider whether the PLC needs to interface with external systems or devices. High-level languages like Structured Text or even C/C++ are well-suited for implementing communication protocols and integrating with other software platforms.
- Future Expansion: Think about the scalability and flexibility of the chosen language. Will it accommodate future changes and expansions in the automation system without requiring significant rework?
- Industry Standards: Depending on the industry and application, there might be specific programming language standards or best practices that are recommended or required. It’s important to adhere to these standards to ensure compliance and interoperability.
- Vendor Support: Different PLC vendors provide different programming environments and language options. Evaluate the capabilities and support offered by the PLC manufacturer to ensure a smooth development process.
- Documentation and Resources: Availability of documentation, training materials, and online resources for a specific programming language can significantly impact the efficiency of development and troubleshooting.
In many cases, PLC projects involve a mix of programming languages within a single program. For example, Ladder Logic might be used for basic input/output control, Function Block Diagram for modular components, and Structured Text for complex calculations. This hybrid approach leverages the strengths of each language to create a well-rounded solution.
Selection of a PLC programming language should be a thoughtful process that takes into account the specific requirements, capabilities of the programming team, and the overall goals of the automation project. By carefully considering these factors, engineers can choose the most appropriate language to develop a robust and efficient control system.
Programming Guidelines and Best Practices
PLC (Programmable Logic Controller) programming guidelines and best practices are essential for developing reliable, maintainable, and efficient control systems. Adhering to these guidelines can help streamline the programming process, minimize errors, and ensure the longevity of the automation solution. Here are some key guidelines and best practices to consider:
- Modularity and Reusability:
- Divide the PLC program into modular sections or function blocks that correspond to specific control tasks. This promotes code reusability and simplifies troubleshooting and maintenance.
- Create reusable function blocks for common control logic patterns or frequently used functions. This approach reduces redundant code and speeds up development.
- Structured Programming:
- Follow structured programming principles, such as using well-organized code, meaningful variable and tag names, and consistent indentation. This improves code readability and maintainability.
- Employ appropriate comments and documentation to explain the purpose and functionality of different sections of code. This assists other programmers and future maintainers.
- Consistent Naming Conventions:
- Establish a consistent naming convention for variables, tags, function blocks, and other program elements. Clear and standardized names make it easier to understand the code and minimize confusion.
- Error Handling and Fault Tolerance:
- Implement comprehensive error handling mechanisms to detect and address faults and exceptions. Use error codes, diagnostic messages, and alarms to aid in troubleshooting.
- Incorporate fault-tolerant design principles to ensure that the system can handle unexpected situations without catastrophic failures.
- Safety Considerations:
- Prioritize safety by implementing fail-safe and fail-to-safe logic where appropriate. Design the system to return to a safe state in case of failures.
- Implement safety interlocks and overrides to prevent unsafe conditions or operations.
- Testing and Simulation:
- Thoroughly test the PLC program in a simulation environment before deploying it to the actual equipment. This helps identify and rectify errors without disrupting operations.
- Use simulation tools to replicate real-world conditions and scenarios, ensuring that the control logic functions as intended.
- Documentation and Version Control:
- Maintain detailed documentation that includes the program’s purpose, design, and operational procedures. This documentation is invaluable for troubleshooting, maintenance, and future enhancements.
- Implement version control for the PLC program to keep track of changes and updates over time. This prevents unintentional regressions and allows for easy rollback if necessary.
- Performance Optimization:
- Optimize the program for performance by minimizing scan times, reducing unnecessary calculations, and optimizing memory usage. Efficient programs lead to quicker response times and better system performance.
- Avoiding Common Pitfalls:
- Avoid using complex or convoluted logic that might be difficult to understand or troubleshoot.
- Be cautious of excessive nesting in control structures, as it can lead to confusion and errors.
- Steer clear of relying solely on one programming language; use the appropriate language for each specific task.
- Regular Maintenance and Updates:
- Establish a maintenance schedule to review and update the PLC program as needed. Equipment changes, process adjustments, and other factors may require modifications to the control logic.
- Keep up to date with the latest software updates and patches from the PLC manufacturer to ensure compatibility and security.
- Training and Skill Development:
- Invest in training for programmers and engineers to ensure they are proficient in the chosen programming languages and best practices.
- Foster a culture of continuous learning and improvement within the programming team.
By adhering to these PLC programming guidelines and best practices, engineers can create robust, efficient, and maintainable control systems that meet the needs of industrial automation while minimizing errors and downtime.
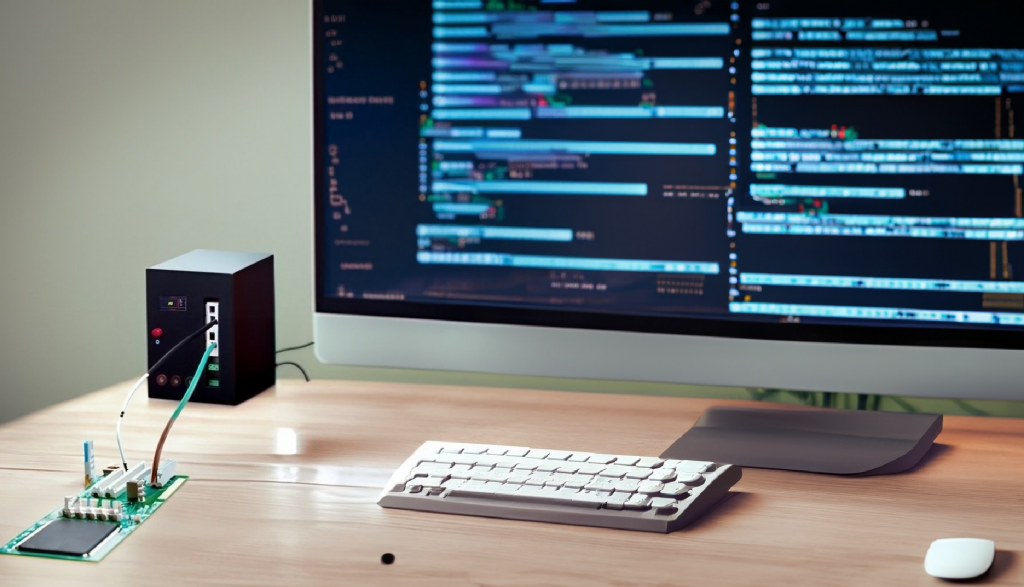
Specialized Languages and Standards
In addition to the commonly used PLC programming languages, there are specialized languages and standards that cater to specific industries, applications, or requirements. These specialized languages and standards provide tailored solutions for unique challenges in automation and control systems. Here are some examples:
- Function Block Diagram (FBD):
- In the context of safety-critical applications, such as nuclear power plants, the IEC 61508 standard introduces a variation of Function Block Diagrams known as “Safety Function Block Diagrams” (SFBD). These diagrams emphasize safety-related aspects, including redundant systems, diagnostics, and fault tolerance.
- Structured Text (ST) and Sequential Function Chart (SFC):
- For applications in the process industry, the IEC 61131-3 standard defines a set of languages suitable for programming safety functions in accordance with the IEC 61511 standard. This includes using Structured Text and Sequential Function Chart to develop safety-related logic.
- Continuous Function Chart (CFC):
- The IEC 61499 standard introduces the Continuous Function Chart language, which is used to describe the behavior of distributed control systems. It allows for the modeling of dynamic interactions between components in a distributed control environment.
- Motion Control Languages:
- In robotics and motion control applications, specialized languages like RAPID (ABB robots) and KRL (KUKA robots) are used to program robot motion paths and tasks. These languages offer commands for controlling robot movements, trajectories, and interactions.
- IEC 61131-3 Standard:
- The IEC 61131-3 standard defines a set of programming languages for programmable controllers. These languages include Ladder Diagram (LD), Function Block Diagram (FBD), Structured Text (ST), Instruction List (IL), and Sequential Function Chart (SFC). This standard provides consistency in programming across different manufacturers’ PLCs.
- IEC 61850 Standard:
- IEC 61850 is a standard for communication networks and systems in substations and power grids. It defines communication protocols, data models, and engineering processes for power system automation and protection.
- PLCopen Standard:
- PLCopen is an organization that promotes standardization in industrial control programming. They define guidelines and best practices for using IEC 61131-3 languages, as well as motion control and safety-related programming.
- Batch Control Languages:
- In industries like pharmaceuticals and chemicals, batch control languages are used to manage and automate complex batch processes. These languages ensure precise execution of procedures, tracking of raw materials, and compliance with regulatory requirements.
- Automotive Standards:
- The automotive industry often uses specialized languages to program PLCs and controllers for manufacturing processes, quality control, and assembly line automation. These languages ensure efficient and reliable production in high-volume manufacturing.
- Process Visualization Standards:
- While not programming languages, standards like OPC (OLE for Process Control) facilitate communication between various automation devices and software applications, allowing data exchange and visualization in a unified manner.
These specialized languages and standards cater to specific industries and applications, ensuring that control systems meet unique requirements and adhere to industry-specific regulations. By using these specialized tools, engineers can develop automation solutions that are optimized for safety, efficiency, and reliability in their respective domains.
Conclusion
In the realm of industrial automation, PLC programming languages serve as the cornerstone of control, enabling engineers to orchestrate complex processes, streamline operations, and ensure the reliability of machinery and systems. The journey of PLC programming languages has seen a remarkable progression, from the introduction of Ladder Logic, reminiscent of traditional relay logic, to the diversified landscape of textual languages like Structured Text and high-level languages catering to diverse industries and applications.
The evolution of PLC programming languages reflects the ever-growing demands of industries, necessitating more than just relay-based control. These languages have adapted to encompass safety-critical considerations, modular design principles, advanced mathematical calculations, and seamless integration with the modern digital ecosystem. Through each stage, the focus has remained on improving efficiency, maintainability, and system performance.
As industrial automation continues to embrace cutting-edge technologies such as IoT, AI, and cloud computing, PLC programming languages are positioned to further evolve. This evolution will likely entail even more powerful programming capabilities, real-time data analysis, and greater interoperability between various devices and systems.
PLC programming languages stand as a testament to human ingenuity, shaping the way industries operate and innovate. By harnessing these languages, engineers wield the ability to control the intricate dance of machines, optimizing processes and ushering in a future where automation is not just a necessity, but a driving force for progress.