Process control is a fundamental discipline that plays a pivotal role in a wide range of industries, from manufacturing and chemical production to energy generation and pharmaceuticals. At its core, process control involves the management and regulation of various parameters within a system to ensure that desired outcomes are consistently achieved. These outcomes can encompass factors such as product quality, operational efficiency, safety, and resource utilization.
The primary objective of process control is to maintain a system’s variables within specific limits or setpoints, thereby minimizing deviations and fluctuations that might lead to undesirable outcomes. This is achieved through the implementation of control strategies that utilize various sensors, actuators, feedback loops, and computational algorithms. By continuously monitoring the system’s conditions and making real-time adjustments, process control ensures that the system remains stable, efficient, and capable of meeting predefined objectives.
Process control concepts can be broadly categorized into two main types: open-loop control and closed-loop control. Open-loop control involves setting a predetermined input without actively measuring the system’s output. This approach is simple but lacks adaptability to changing conditions. Closed-loop control, on the other hand, incorporates feedback mechanisms, constantly measuring the system’s output and adjusting the input to maintain desired conditions. This results in greater accuracy and robustness, making it the preferred choice for complex and critical processes.
In this exploration of process control concepts, we will delve into the key principles that underpin this field. We will examine the roles of sensors and actuators in gathering and responding to data, the significance of feedback loops in maintaining stability, and the various control strategies ranging from classical PID (Proportional-Integral-Derivative) control to more advanced model-based and adaptive control techniques. Furthermore, we will highlight the importance of process modeling, simulation, and optimization in refining control strategies and improving overall system performance.
Whether it’s ensuring the consistent production of high-quality goods, optimizing the efficiency of chemical reactions, or maintaining safe and reliable operations in industrial settings, a solid understanding of process control concepts is essential. As industries become more complex and technology-driven, the mastery of these concepts becomes increasingly valuable in achieving precision, reliability, and innovation in various processes.
Fundamentals of Process Control
Process control is a multidisciplinary field that draws upon principles from engineering, mathematics, and technology to manage and regulate the behavior of dynamic systems. It involves manipulating various parameters within a system to achieve desired outcomes while minimizing deviations and disturbances. The fundamentals of process control encompass a range of concepts, methodologies, and techniques aimed at maintaining stability, optimizing performance, and ensuring the consistency of processes in diverse industries. Let’s delve into some of the key fundamentals:
- Control Systems and Components: Control systems are at the heart of process control. They consist of various components, including sensors, actuators, controllers, and feedback loops. Sensors gather data from the system, which is then used to make informed decisions. Actuators adjust the system’s inputs based on the controller’s instructions. The feedback loop continuously compares the system’s actual output to the desired setpoint and makes adjustments accordingly.
- Open-Loop and Closed-Loop Control: Open-loop control involves setting a predefined input without considering the system’s output. It’s a simple approach but lacks adaptability to changes and disturbances. Closed-loop control, also known as feedback control, is more sophisticated. It involves continuously measuring the system’s output and adjusting the input to maintain desired conditions. Closed-loop control is more accurate and resilient to disturbances.
- Setpoints and Reference Values: Setpoints are the desired values or conditions that a system aims to achieve. They serve as a reference for the control system to adjust the inputs. For instance, in temperature control, the setpoint might be the desired temperature of a reactor. The control system then works to keep the actual temperature as close to the setpoint as possible.
- Feedback Control Strategies: Feedback control strategies are designed to maintain stability and reduce deviations from the setpoint. The proportional-integral-derivative (PID) controller is a widely used feedback control algorithm. Proportional control adjusts the input in proportion to the error (deviation from the setpoint). Integral control considers accumulated past errors, and derivative control accounts for the rate of change of the error.
- Feedforward Control: While feedback control reacts to deviations after they occur, feedforward control anticipates disturbances and adjusts the input proactively. It uses predictive models to estimate how disturbances will affect the system and applies corrective actions in advance.
- Process Modeling and Simulation: Process models are mathematical representations of a system’s behavior. They help understand how different factors interact and predict how the system will respond to changes. Simulation involves running these models to observe and analyze the system’s behavior under different conditions, aiding in the design and tuning of control strategies.
- Advanced Control Techniques: As processes become more complex, advanced control techniques come into play. Model-based control utilizes mathematical models of the system to optimize performance. Adaptive control adjusts the control parameters in real-time based on changing conditions. Predictive control uses predictive models to anticipate system behavior and optimize inputs accordingly.
- Process Optimization: Process control and optimization often go hand in hand. Optimization seeks to find the best possible set of input values to achieve desired outcomes. This could involve maximizing efficiency, minimizing costs, or ensuring product quality.
Fundamentals of process control form the foundation for effectively managing complex systems and processes across industries. By understanding and applying these principles, engineers and professionals can enhance system stability, efficiency, and overall performance.
Control Loops and Block Diagrams
Control loops and block diagrams are essential concepts in the field of process control, enabling engineers and practitioners to design, analyze, and optimize control systems for a wide range of applications. These tools provide a visual representation of how various components interact within a control system and help in understanding the flow of information and actions.
Control Loops:
A control loop is a fundamental structure that consists of several interconnected components working together to achieve a specific control objective. The primary components of a control loop are:
- Process or Plant: This is the system or process that requires control. It could be a chemical reactor, a manufacturing assembly line, a temperature-controlled environment, or any other dynamic system.
- Sensor: The sensor measures a relevant parameter or variable of the process, such as temperature, pressure, flow rate, or level. The measured data is sent to the controller for analysis.
- Controller: The controller processes the data received from the sensor and generates control actions. It compares the actual process variable (PV) with the desired setpoint (SP) and computes the appropriate control output.
- Actuator: The actuator receives the control signal from the controller and adjusts the system’s inputs, such as adjusting a valve, changing a motor speed, or altering a heating element.
- Feedback Loop: The feedback loop is responsible for closing the loop and maintaining the desired process variable close to the setpoint. The controller continuously adjusts the actuator based on the feedback from the sensor.
Block Diagrams:
Block diagrams are graphical representations that illustrate the relationships between the different components of a control system. They use blocks to represent various components and lines to represent the flow of signals or information. Block diagrams provide a clear and concise way to visualize the structure and behavior of complex control systems.
In a block diagram, each block represents a functional component, and arrows connecting the blocks indicate the flow of signals or information. Key elements of block diagrams include:
- Summing Points: Represented by a circle with plus or minus signs, summing points indicate where different signals are added or subtracted. These points often correspond to the error signals that drive the controller’s actions.
- Transfer Functions: Transfer functions describe the relationship between input and output signals for each block. They capture the behavior of the component in terms of mathematical equations.
- Feedback Paths: Feedback paths are indicated by arrows that loop back to earlier components in the diagram. These paths represent the flow of feedback signals, which play a crucial role in maintaining control stability.
- Gain Blocks: Gain blocks represent the amplification or attenuation of signals. They are often used to model the effect of controllers, sensors, and actuators on the signals.
Block diagrams offer a systematic way to analyze the behavior of control systems, enabling engineers to predict how changes in one component will affect the overall system response. They facilitate the design and tuning of control strategies and provide insights into system dynamics, stability, and performance.
Control loops and block diagrams are foundational tools in the field of process control. They provide a visual representation of the interaction between components within a control system, helping engineers design effective control strategies, optimize system performance, and ensure stability in a wide range of industrial processes.
Types of Control Strategies
In the realm of process control, various strategies are employed to regulate and manage systems in order to achieve desired outcomes. These strategies encompass a spectrum of techniques, each suited to different scenarios and objectives. Here, we’ll explore some of the primary types of control strategies used across industries:
- Proportional Control (P-Control): Proportional control adjusts the control output in direct proportion to the error, which is the difference between the desired setpoint and the actual process variable. This type of control provides quick response to changes but may result in steady-state error (the system not reaching the exact setpoint).
- Integral Control (I-Control): Integral control focuses on eliminating steady-state error. It integrates the cumulative error over time and adjusts the control output accordingly. This is particularly useful when small, continuous deviations from the setpoint are unacceptable.
- Derivative Control (D-Control): Derivative control takes into account the rate of change of the error. It helps dampen rapid changes and can improve stability by anticipating future errors based on the error’s current rate of change.
- Proportional-Integral-Derivative (PID) Control: PID control combines proportional, integral, and derivative actions to strike a balance between fast response, zero steady-state error, and stable control. It’s one of the most widely used control strategies due to its versatility and effectiveness.
- On-Off Control (Bang-Bang Control): On-off control involves turning the control output fully on or off based on whether the process variable is above or below the setpoint. While simple, it can result in frequent switching and may not be suitable for processes sensitive to large fluctuations.
- Feedforward Control: Feedforward control anticipates disturbances and adjusts the control output before the actual process variable deviates from the setpoint. It’s particularly valuable when disturbances are known and predictable.
- Cascade Control: Cascade control involves multiple control loops. An outer loop adjusts a manipulated variable to achieve a desired setpoint for an intermediate process variable. The output of the outer loop then becomes the setpoint for an inner loop that controls the actual process variable.
- Ratio Control: Ratio control maintains a specific ratio between two process variables, even if their absolute values change. This is valuable in processes where maintaining a consistent ratio is critical.
- Model Predictive Control (MPC): MPC uses a predictive model of the process to optimize the control inputs over a future time horizon. It considers constraints on variables and inputs, making it suitable for complex processes with constraints.
- Adaptive Control: Adaptive control adjusts control parameters based on changing process conditions or disturbances. It’s useful when the dynamics of the process change over time.
- Fuzzy Logic Control: Fuzzy logic control uses linguistic variables and rules to mimic human decision-making processes. It’s effective when the system behavior is complex and not well-defined by mathematical models.
- Neural Network Control: Neural network control employs artificial neural networks to learn and approximate the system’s behavior. It’s particularly useful when the process is nonlinear and difficult to model.
Each type of control strategy has its strengths and limitations, making it suitable for specific scenarios. Often, a combination of strategies is used to achieve optimal control performance while considering factors such as stability, responsiveness, disturbance rejection, and energy efficiency. The choice of strategy depends on the nature of the process, the control objectives, and the available resources and technology.
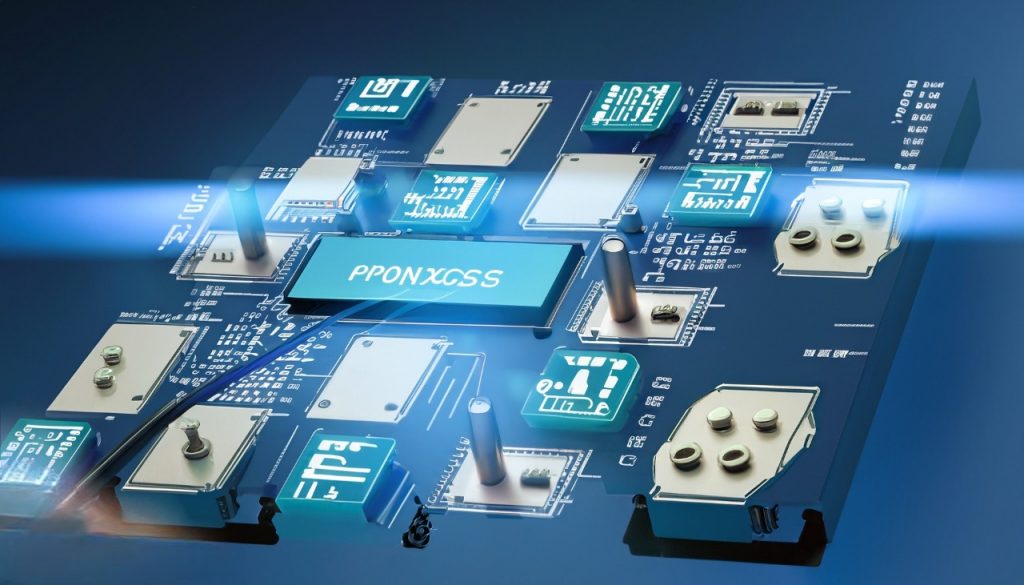
Control System Dynamics
Control system dynamics are at the core of understanding how systems respond to changes and how control strategies influence their behavior. Dynamics refer to the time-based evolution of a system’s state or output in response to inputs, disturbances, or changes in the environment. In the context of process control, understanding control system dynamics is crucial for designing effective control strategies, predicting system behavior, and ensuring stability.
Key Concepts:
- Time Delays: Time delays are often present in real-world systems due to factors such as sensor response time, actuator response time, and transportation delays in the system. Time delays can introduce challenges to control as they can lead to oscillations, instability, or reduced performance.
- Lag and Lead: Systems can exhibit lag or lead behavior. Lag refers to a delay in the response of the output to changes in the input. Lead behavior occurs when the output responds faster than the input. Both lag and lead behavior can impact the stability and transient response of a control system.
- Transient Response: The transient response is the behavior of the system as it approaches a new equilibrium after a change in input or setpoint. It includes characteristics such as rise time (time taken to reach 90% of the new value), overshoot (exceeding the new value temporarily), and settling time (time to reach a stable value within a certain tolerance).
- Steady-State Response: The steady-state response is the behavior of the system once it has settled into a stable state. It’s important to ensure that the system reaches the desired steady-state and maintains it consistently.
- Frequency Response: Frequency response analysis examines how a system responds to sinusoidal inputs at different frequencies. It provides insights into the system’s stability, amplification, and phase shift at various frequencies.
- Bode Plots: Bode plots are graphical representations of a system’s frequency response, showing the gain and phase shift as functions of frequency. They help analyze stability and performance characteristics across different frequency ranges.
Importance of Understanding Dynamics:
- Stability Analysis: Control system dynamics play a critical role in determining the stability of a system. Understanding how inputs, disturbances, and control actions influence the system’s behavior helps identify conditions under which a system remains stable or becomes unstable.
- Controller Tuning: Effective control system tuning requires a grasp of system dynamics. Proper tuning ensures that the system responds quickly to changes while avoiding overshooting, oscillations, or slow responses.
- Disturbance Rejection: Knowledge of dynamics helps design control strategies that can reject disturbances and maintain desired setpoints even in the presence of external changes.
- Predictive Modeling: Dynamics understanding enables the creation of accurate predictive models. These models help simulate and analyze how a system will respond to various inputs and disturbances.
- Troubleshooting: When a control system behaves unexpectedly, understanding dynamics aids in diagnosing issues and implementing corrective measures.
- Optimization: Dynamics information is crucial for optimizing control strategies, ensuring that the system operates efficiently while meeting performance objectives.
Control system dynamics form the bridge between theoretical control concepts and practical implementation. They allow engineers and practitioners to fine-tune control strategies, adapt them to changing conditions, and ensure that systems operate reliably and efficiently.
Instrumentation and Sensors
Instrumentation and sensors are the eyes and ears of process control systems, providing crucial data that enable engineers to monitor, analyze, and regulate industrial processes. These components play a pivotal role in various industries, from manufacturing and chemical production to energy generation and environmental monitoring. They ensure that processes run efficiently, safely, and with high product quality. Let’s delve into the significance of instrumentation and sensors in process control:
Instrumentation:
Instrumentation refers to the collection of devices and equipment used to measure, monitor, control, and analyze various process variables. These variables can include physical parameters such as temperature, pressure, flow rate, level, pH, conductivity, and more. Instrumentation systems consist of several key components:
- Sensors: Sensors are devices that convert physical quantities (such as temperature or pressure) into electrical signals that can be easily measured and processed. Different types of sensors are designed to sense specific variables, and their accuracy and reliability are critical for accurate process control.
- Transmitters: Transmitters amplify and convert the weak electrical signals from sensors into more robust signals suitable for transmission over longer distances. They often include signal conditioning to ensure accuracy and consistency.
- Controllers: Controllers receive signals from sensors or transmitters, compare them to desired setpoints, and generate control actions to maintain the process variable within acceptable limits. Controllers use algorithms and logic to compute these actions.
- Actuators: Actuators are devices responsible for implementing control actions in the process. They receive control signals from controllers and adjust valves, pumps, motors, or other mechanisms to regulate the process variable.
- Display and User Interface: Instruments often include displays that show real-time process data and control parameters. User interfaces allow operators to interact with the control system, set parameters, and monitor process conditions.
Sensors:
Sensors are the heart of instrumentation systems, providing the critical data needed for process control. They come in a wide variety of types, each designed to measure specific physical properties. Some common types of sensors include:
- Temperature Sensors: Thermocouples, resistance temperature detectors (RTDs), and thermistors measure temperature variations. They are vital for maintaining consistent reaction conditions and preventing overheating.
- Pressure Sensors: Pressure sensors monitor fluid or gas pressure and are used in systems where maintaining specific pressure levels is crucial for safety and efficiency.
- Flow Sensors: Flow sensors measure the rate of fluid or gas flow within a system. They are used in applications such as monitoring liquid movement in pipelines or regulating gas flow rates.
- Level Sensors: Level sensors determine the fill level of liquids or solids in tanks, vessels, or containers. They help prevent overflows and ensure proper resource management.
- pH Sensors: pH sensors measure the acidity or alkalinity of solutions. They are essential in industries such as chemical processing, food and beverage production, and water treatment.
- Conductivity Sensors: Conductivity sensors measure the ability of a solution to conduct electrical current, providing insights into the concentration of dissolved ions.
- Gas Sensors: Gas sensors detect the presence and concentration of specific gases in the environment. They are crucial for monitoring air quality and detecting hazardous gases.
- Position Sensors: Position sensors determine the position of mechanical components in a system. They are used in applications such as robotics and motion control.
The accuracy, reliability, and responsiveness of sensors are paramount in process control. Proper calibration, maintenance, and selection of appropriate sensor types are essential to ensure that the data collected accurately reflects the state of the process.
In conclusion, instrumentation and sensors are indispensable components of process control systems. They enable engineers and operators to gain insights into the behavior of industrial processes, make informed decisions, and implement effective control strategies to ensure optimal efficiency, safety, and quality in various industries.
Challenges and Future Trends in Process Control
Process control plays a critical role in ensuring efficient, safe, and high-quality operation of industrial processes. As industries evolve and technology advances, new challenges emerge, prompting the development of innovative solutions and the emergence of future trends. Here are some of the key challenges and future trends in process control:
Challenges:
- Complexity and Scale: Modern processes are becoming increasingly complex and larger in scale. Managing intricate systems with numerous interacting variables poses challenges in terms of control strategy design, implementation, and optimization.
- Nonlinear Systems: Many processes exhibit nonlinear behavior that cannot be accurately described by linear models. Nonlinearities introduce complexities in control design, as traditional linear control techniques may be insufficient.
- Uncertainty and Disturbances: External factors such as changing environmental conditions, raw material variations, and equipment wear can introduce uncertainty and disturbances in processes. Effective control strategies need to account for these uncertainties.
- Cybersecurity: With the increasing integration of digital technologies, process control systems are vulnerable to cyber threats. Ensuring the security and integrity of control systems becomes a critical challenge to prevent unauthorized access, data breaches, and system disruptions.
- Energy Efficiency: Industries are under pressure to improve energy efficiency and reduce carbon emissions. Achieving energy-efficient operations while maintaining product quality requires advanced control strategies and optimization techniques.
- Human-Machine Interaction: As control systems become more complex, the interface between operators and control systems becomes crucial. Designing intuitive user interfaces and operator training programs is essential to avoid errors and improve decision-making.
Future Trends:
- Data-Driven Control: The integration of data analytics and machine learning into process control is on the rise. Data-driven models can capture complex relationships and enable predictive maintenance, anomaly detection, and adaptive control strategies.
- Advanced Process Modeling: Improved modeling techniques, including dynamic and predictive models, enhance the accuracy of control strategies. These models can capture intricate process behaviors and optimize control actions.
- Distributed and Decentralized Control: Decentralized control approaches distribute decision-making among different control units, increasing system resilience and adaptability. This trend is particularly relevant in industries with interconnected and distributed processes.
- Smart Sensors and IoT: Internet of Things (IoT) devices and smart sensors enable real-time data collection and communication. This data can be utilized for better process understanding, optimization, and remote monitoring.
- Model Predictive Control (MPC): MPC is evolving with improved algorithms and computational power. It enables the optimization of control actions over a future time horizon, accounting for constraints and disturbances.
- Digital Twins: Digital twins are virtual replicas of physical processes, providing a platform for simulation, testing, and optimization. They allow for more efficient process design, monitoring, and troubleshooting.
- Robust and Adaptive Control: Robust control strategies can handle uncertainties and disturbances, while adaptive control techniques adjust control parameters based on changing process conditions.
- Sustainability and Green Processes: Future trends emphasize sustainable practices and green technologies. Process control will play a crucial role in optimizing resource utilization, minimizing waste, and achieving environmental goals.
In conclusion, the field of process control continues to evolve to meet the challenges posed by modern industries. Future trends are centered around data-driven approaches, advanced modeling, decentralized control, and sustainability. As technologies like AI, IoT, and advanced analytics become more prominent, the potential for innovative and efficient process control strategies grows, ultimately benefiting industries, the environment, and society at large.
Conclusion
Concepts of process control form the backbone of effective and efficient industrial operations across a multitude of sectors. Through the intricate interplay of process variables, setpoints, sensors, actuators, controllers, and feedback loops, process control systems enable the precise management of complex systems. By maintaining variables within desired ranges, these systems ensure product quality, safety, and resource optimization.
The dichotomy between open-loop and closed-loop control, along with the nuances of proportional, integral, and derivative control modes, underscores the importance of striking a balance between stability and responsiveness. Furthermore, the continuous evolution of control strategies, from traditional PID control to advanced techniques like model predictive and adaptive control, reflects the dynamic nature of industrial processes and the ever-increasing demand for precision and efficiency.
As industries continue to embrace digitalization and automation, the future of process control lies in harnessing the power of data-driven approaches, artificial intelligence, and interconnected systems. These trends promise enhanced predictive capabilities, improved resource utilization, and quicker response times to changing conditions.
In essence, the concepts of process control constitute a roadmap for maintaining control over the unpredictable. They empower industries to navigate the complexities of their operations, optimize processes, and ultimately ensure the consistency and excellence of the products and services they deliver.