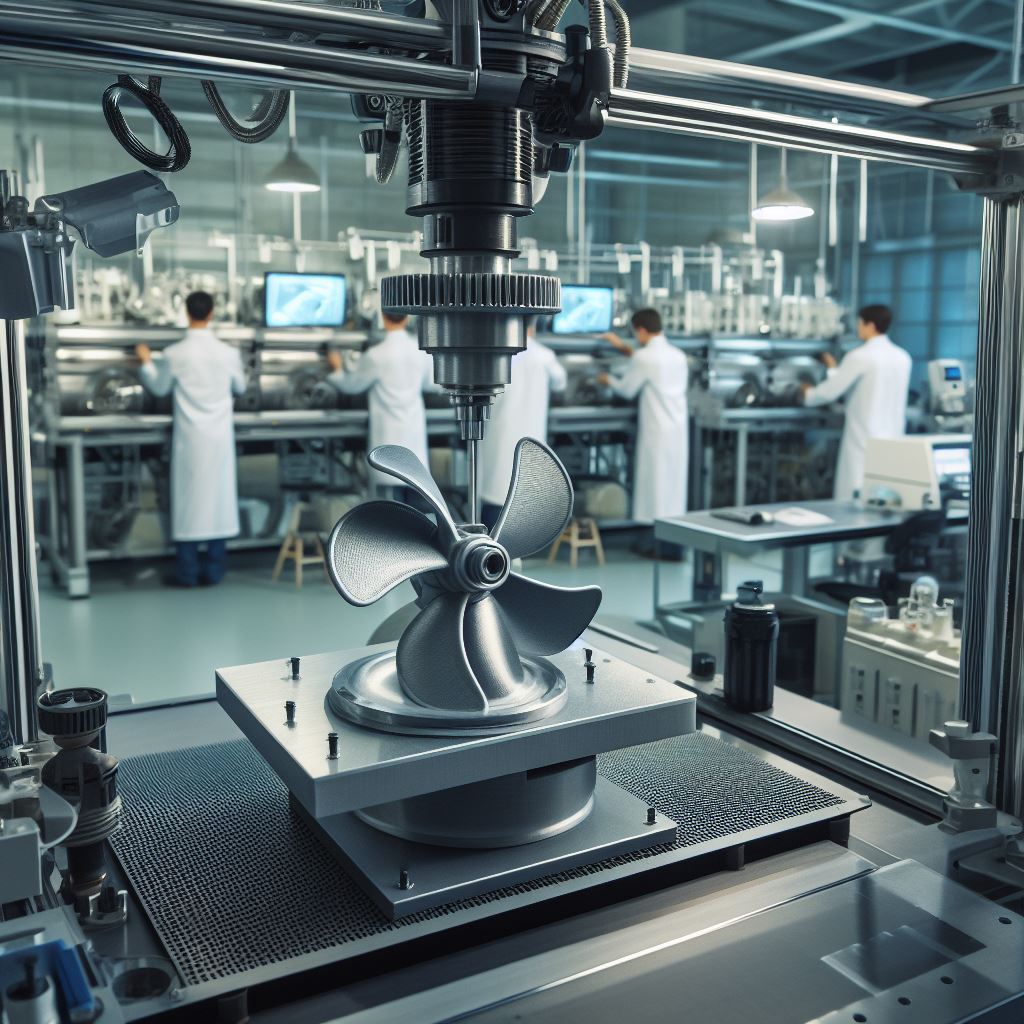
In today’s ever-evolving technological landscape, 3D printing, also known as additive manufacturing, has emerged as a game-changer across various industries. It has revolutionized the way companies design, prototype, and produce parts, leading to increased efficiency, cost savings, and unparalleled design possibilities. From aerospace and defense to medical and dental, and from consumer goods to industrial applications, 3D printing is reshaping industries and driving innovation.
CHAPTER 1: Aerospace & Defense
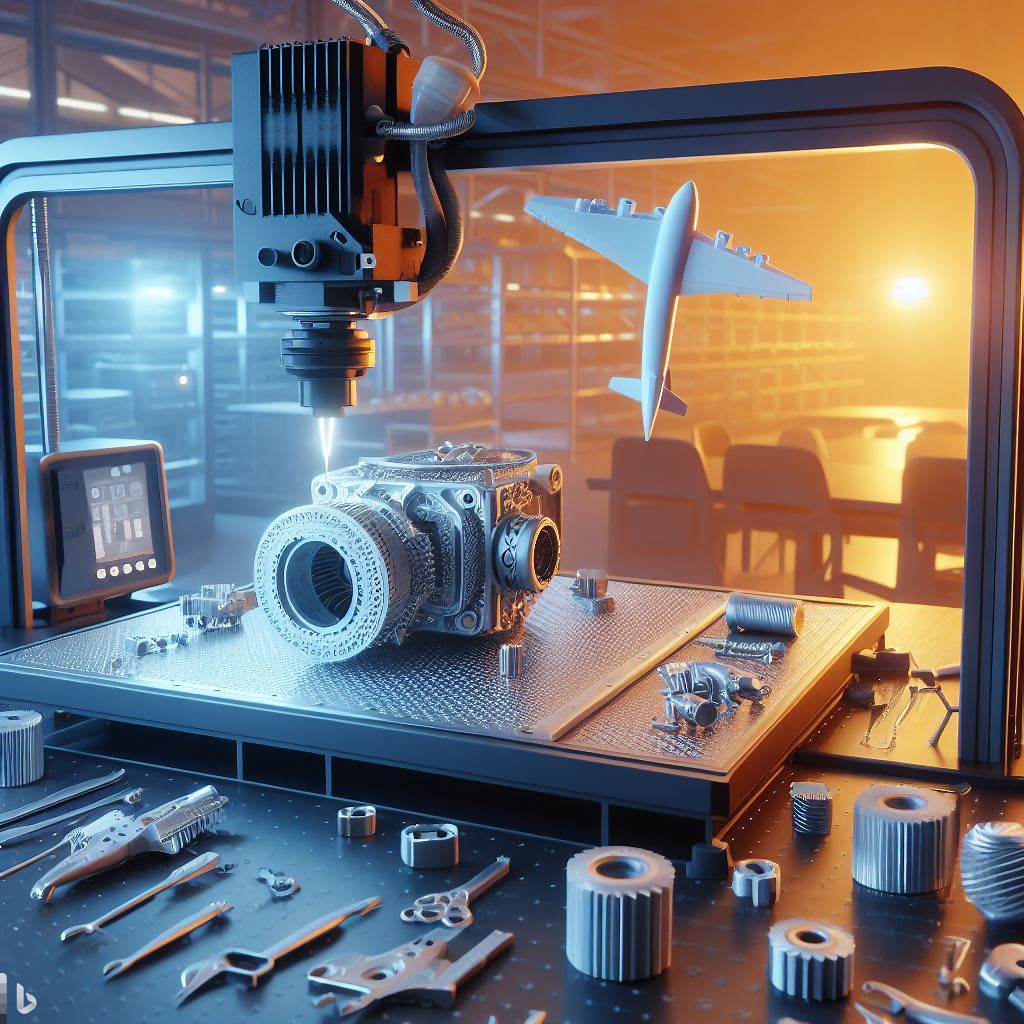
Pioneering the Adoption of 3D Printing
The aerospace and defense industry has been at the forefront of 3D printing adoption since its inception in the late 1980s. Major players in the industry, including GE, Airbus, Boeing, Safran, and GKN, have recognized the immense value that 3D printing brings to their operations. As a result, the aerospace and defense sector currently represents a significant share of the $10.4 billion additive manufacturing market.
Beyond Prototypes: Functional Parts Taking Flight
While 3D printing started as a tool for rapid prototyping, it has now advanced to the point where functional parts are being 3D printed and used in aircraft. The technology allows for the production of complex geometries without the need for expensive tooling equipment. Examples of 3D-printed aerospace components include air ducts (SLS), wall panels (FDM), and even structural metal components (DMLS, EBM, DED).
The Benefits of 3D Printing in Aerospace & Defense
The aerospace industry, with its requirement for highly complex parts produced in low volumes, greatly benefits from 3D printing. The technology enables cost-effective production of small batches of parts without the need for extensive tooling. Additionally, 3D printing allows for weight reduction, which is crucial for improving aircraft performance and reducing fuel consumption. The process also minimizes material waste, offers part consolidation opportunities, and facilitates maintenance and repair operations.
Real-World Applications
One remarkable example of 3D printing in the aerospace industry is the production of rocket components. Engineers are leveraging 3D printing, particularly with metals, to innovate the design and manufacture of rocket parts, significantly reducing production time. For instance, ArianeGroup, a joint venture of Airbus Group and Safran, developed a 3D-printed injector head for the Ariane 6 launcher, reducing 248 components down to a single 3D-printed part. This achievement resulted in a cost reduction of 50% and a production time decrease from three months to just 35 hours.
Enhancing Aircraft Interiors
Aircraft interiors, including cabin components, can also benefit from 3D printing. Airbus, for example, has utilized 3D printing to produce spacer panels for its A320 aircraft. Traditional manufacturing methods, such as injection molding, were costly and complex for low-volume production and specialized requirements. With 3D printing, Airbus was able to create lightweight, customized spacer panels with complex lattice structures, resulting in a 15% weight reduction.
Repairing and Maintaining Aerospace Equipment
The maintenance, repair, and overhaul (MRO) function is critical in the aerospace industry due to the long lifespan of aircraft. 3D printing plays a significant role in MRO activities, with metal 3D printing technologies like Direct Energy Deposition being used to repair aerospace and military equipment. Turbine blades and other high-end components can also be restored and repaired through the addition of material to worn-out surfaces, extending the life of valuable assets.
CHAPTER 2: Automotive
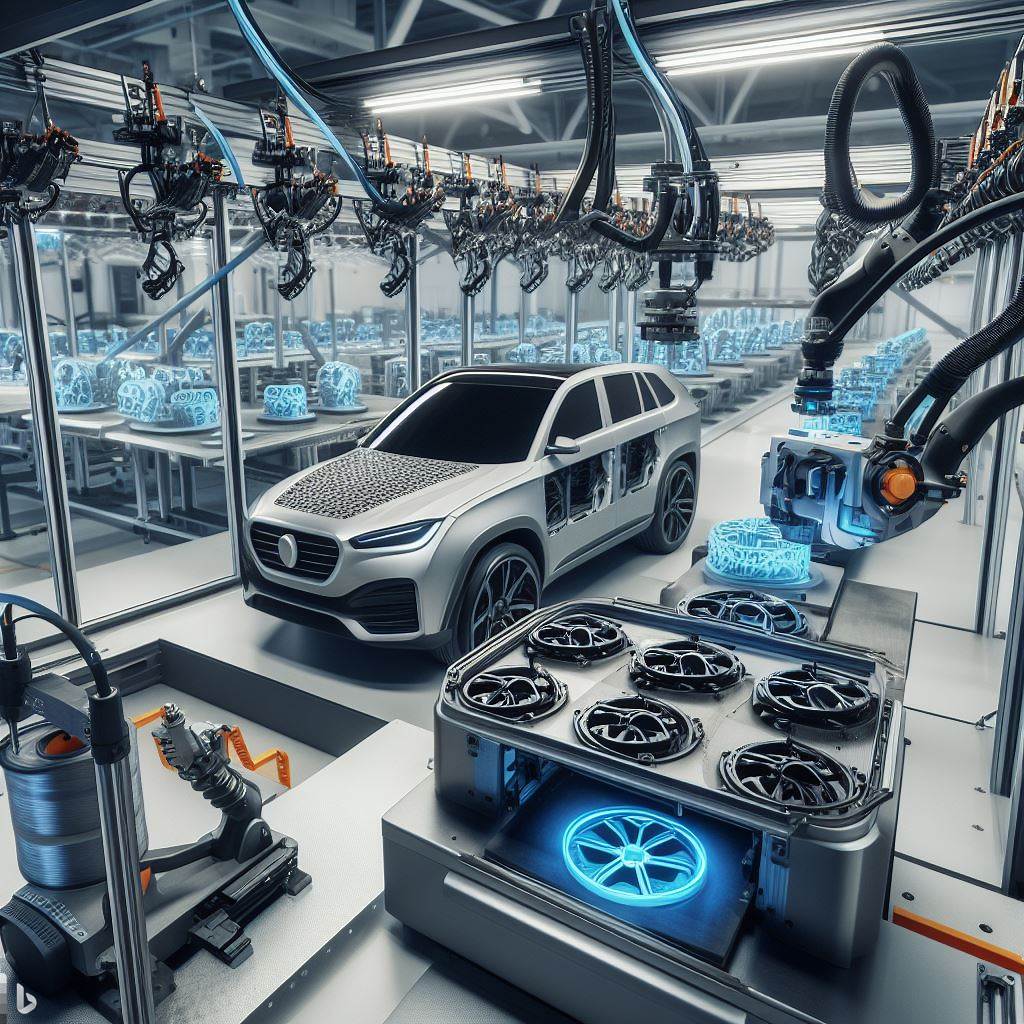
Driving Innovation in the Automotive Industry
The automotive industry is increasingly recognizing the value of additive manufacturing, with global automotive AM revenues reaching $1.4 billion in 2019. This figure is expected to rise to $5.8 billion by 2025. While 3D printing is widely used for prototyping, automotive companies are exploring innovative applications such as tooling and end-use parts, signaling exciting developments for the sector.
Accelerating Product Development
Prototyping is a crucial part of the automotive product development process, enabling designers and engineers to test and validate parts before manufacturing. 3D printing accelerates product development cycles by offering a quick and cost-effective approach to designing and producing parts. Eliminating the need for tooling equipment, this technology allows for rapid design iterations and quick modifications.
Greater Design Flexibility
The ability to produce designs quickly gives automotive designers greater flexibility in testing multiple design options. 3D printing enables quick design changes and modifications, allowing designers to explore various possibilities in a fraction of the time.
Customization and Complex Geometries
3D printing offers automakers a cost-effective and flexible solution for producing customized parts. In luxury and motorsports segments, companies are leveraging 3D printing to produce personalized interior and exterior parts. Additionally, 3D printing enables the production of complex geometries, including internal channels for conformal cooling, thin walls, and fine meshes, resulting in lightweight yet durable parts.
Real-World Applications
Leading automotive companies have embraced 3D printing to enhance their products and manufacturing processes. For example, Porsche has introduced 3D-printed custom seats for its sports cars, leveraging the technology to provide personalized seating options. Adidas has revolutionized footwear production by 3D printing midsoles for its Futurecraft 4D sneakers, allowing for improved performance and design possibilities.
Tooling Innovations
The automotive industry benefits from 3D printing by using the technology to produce custom tooling equipment such as jigs and fixtures on demand. This approach reduces lead times and costs while improving functionality. French aerospace manufacturer Latécoère and the Moog Aircraft Group have both realized significant time and cost savings by utilizing 3D printing for the production of custom tooling equipment.
On-Demand Production of Spare Parts
Additive manufacturing enables the production of spare parts quickly and cost-effectively, reducing the need for vast inventories and long lead times. Satair, an Airbus subsidiary specializing in spare parts distribution, utilizes 3D printing to produce custom parts on demand, simplifying complex supply chain logistics and improving turnaround times for maintenance operations.
CHAPTER 3: Medical & Dental
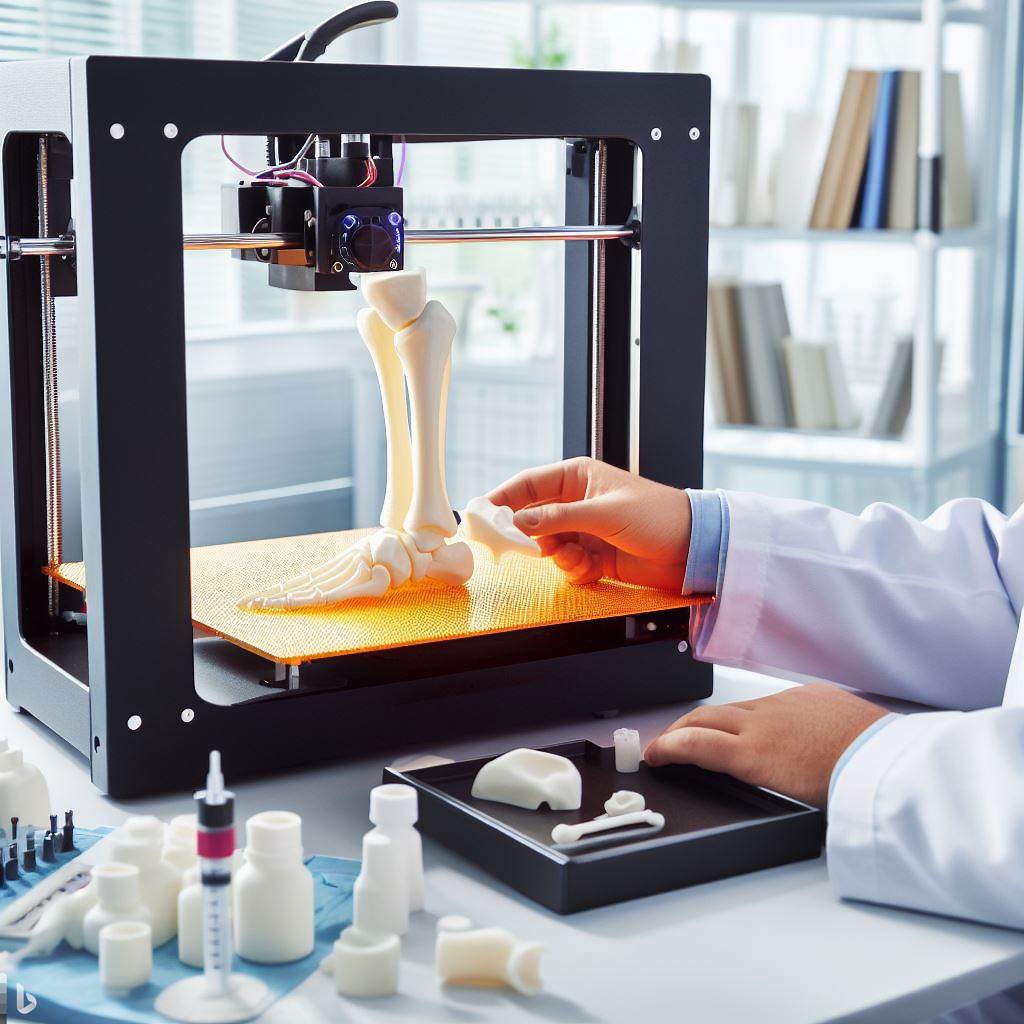
Reshaping the Medical and Dental Industry
The medical and dental industry is experiencing rapid growth in the adoption of additive manufacturing. With its ability to provide personalized patient care cost-effectively, 3D printing is transforming various aspects of the healthcare sector, from medical devices to prosthetics and even bioprinting.
Enhanced Medical Devices
3D printing is an ideal technology for designing and optimizing medical devices. It enables low-cost rapid prototyping, allowing medical device manufacturers to bring new products to market more efficiently. The technology also facilitates the creation of patient-specific devices such as implants and dental appliances.
Customization and Patient-Specific Solutions
The capabilities of 3D printing enable the creation of patient-specific devices, revolutionizing the healthcare industry. Prosthetics and implants can be produced faster and more affordably, improving patient outcomes. Dental labs utilize intraoral scanning and 3D printing to create customized dental products like crowns, bridges, and bite splints, ensuring a perfect fit for each patient.
Real-World Applications
The production of clear aligners is a prime example of 3D printing’s impact on the medical and dental industry. Clear aligners, used to adjust and straighten teeth, are commonly manufactured using 3D-printed molds. This approach allows for cost-effective customization, as each aligner is tailored to the individual patient. Align Technology, the largest producer of clear aligners, relies heavily on 3D printing to produce over half a million unique 3D-printed aligner parts per day.
Bioprinting for regenerative medicine
Although 3D printing cannot yet create fully functional organs, bioprinting has emerged as a promising field within regenerative medicine. By layering living cells, researchers can create artificial tissues and structures that mimic natural tissue characteristics. Bioprinting is already being used to fabricate artificial tissues such as cartilage, skin, bone, blood vessels, and cardiac patches, offering new possibilities for drug testing and personalized medicine.
Surgical Planning and Testing
Hospitals are increasingly utilizing 3D printing to create patient-specific anatomical models for surgical planning and testing. Based on a patient’s MRI and CT scans, these 3D-printed organ replicas assist surgeons in preoperative practice, leading to improved surgical precision and reduced invasiveness. The ability to hold and analyze a physical model greatly enhances surgical outcomes and patient care.
CHAPTER 4: Consumer Goods
The Role of 3D Printing in Consumer-Oriented Industries
Consumer goods companies are recognizing the value of 3D printing as an additive manufacturing solution that meets evolving consumer demands and industrial trends. By accelerating product development, enabling mass customization, and providing design flexibility, 3D printing is reshaping the consumer goods industry, from footwear and beauty products to jewelry and bicycles.
Faster Time-to-Market
The ability to accelerate product development cycles through rapid prototyping is a key advantage of 3D printing in the consumer goods industry. By producing multiple design iterations in a shorter time frame, companies can speed up their time-to-market and stay competitive in a rapidly changing market landscape. Companies like PepsiCo have utilized 3D printing to test and launch new product flavors quickly, reducing development costs and increasing consumer satisfaction.
Mass customization and personalization
Traditional manufacturing processes struggle to produce customized products in small batches efficiently. 3D printing allows for mass customization, enabling consumer goods companies to offer personalized products tailored to individual customer requirements. From customized seating options in sports cars to personalized beauty products, 3D printing provides a cost-effective solution for manufacturing customized consumer goods.
Real-World applications
Leading consumer goods companies have embraced 3D printing to enhance their product offerings and manufacturing processes. Adidas, for instance, utilizes 3D printing to create midsoles for its Futurecraft 4D sneakers, allowing for improved cushioning and performance. French fashion company Chanel has introduced 3D-printed mascara brushes, optimizing the design for better adhesion and performance.
Jewelry and Bicycles
The jewelry industry benefits from 3D printing by producing investment casting patterns and directly printing jewelry using precious metals. 3D printing enables the creation of intricate designs with thin walls and complex details, revolutionizing the customization and production of jewelry. Companies like BOLTENSTERN and Franco Bicycles have leveraged 3D printing to create custom jewelry and 3D-printed composite frames for bicycles, respectively, offering unique designs and improved functionality.
CHAPTER 5: Industrial Goods
Driving innovation in industrial manufacturing
The industrial goods sector, encompassing machinery components and equipment, is undergoing a digital transformation. To maintain operational agility and cost-effectiveness, manufacturers are turning to 3D printing for rapid prototyping, tooling, and end-use parts production. The technology offers design complexity, shorter lead times, and on-demand production capabilities, reshaping the industrial manufacturing landscape.
Design complexity and rapid prototyping
Rapid prototyping is a major use case of 3D printing in the industrial goods sector, allowing for quick design iterations and validation. Manufacturers can implement design changes in a fraction of the time compared to traditional manufacturing methods. 3D printing also enables the production of parts with complex geometries, expanding design possibilities and reducing manufacturing constraints.
Shorter Lead Times and on-demand production
One of the key advantages of 3D printing in the industrial goods sector is its ability to reduce lead times. By eliminating the need for tooling, manufacturers can produce parts more quickly, bypassing time-consuming and costly processes. On-demand production capabilities enable manufacturers to produce parts as needed, reducing inventory costs and ensuring efficient supply chain management.
Real-World applications
Industrial goods companies are embracing 3D printing for various applications, including end-use parts production, tooling innovations, and spare parts manufacturing. Bowman Additive Production, a leading bearings manufacturer, utilizes 3D printing to produce bespoke rollertrain cages, resulting in increased load-bearing capacity and extended working life. Eckhart and Wilson Tool International have also adopted 3D printing for tooling, enabling faster production and improved functionality.
On-Demand production of spare parts
3D printing provides industrial manufacturers with the ability to produce spare parts quickly and cost-effectively. Siemens Mobility, for example, leverages 3D printing to manufacture spare parts and tooling on-demand at its rail service center. This approach reduces costs, improves operational agility, and eliminates the need for extensive spare parts inventories.
CHAPTER 6: The future of 3D Printing
As 3D printing continues to advance, its future looks promising across various industries. The technology is poised to drive further innovation, revolutionize manufacturing processes, and unlock new possibilities. While challenges such as certification and part quality need to be addressed, the potential of 3D printing is just starting to be fully realized.
As additive manufacturing capabilities continue to evolve, industries like aerospace, automotive, medical, dental, consumer goods, and industrial manufacturing will witness further advancements in 3D printing applications. Companies must consider implementing an additive manufacturing strategy to stay competitive and leverage the benefits of this transformative technology.
The future of 3D printing holds immense potential for customization, mass production, and virtual inventories. The technology will enable companies to achieve unprecedented levels of efficiency, agility, and product innovation. As 3D printing continues to shape industries and drive innovation, it is an exciting time for businesses and consumers alike.
Invenio: Your Partner in 3D Printing Implementation
At Invenio, we understand the transformative power of 3D printing and its applications across industries. Whether you need assistance with prototyping in R&D departments or implementing 3D printing techniques on final production and assembly lines, our experts are here to help.
We offer comprehensive solutions and expertise to make your 3D printing journey a success. Stay tuned for our upcoming educational content, where we will delve deeper into the fascinating world of 3D printing.
Check Education section for more details.
What a magnificent article! As Eduardo Hunter, a seasoned truck driver with a deep appreciation for innovation, I am absolutely delighted to share my thoughts on this incredible piece of writing.
As someone who’s spent countless hours on the road, observing the ever-changing landscape of industries and technologies, I can confidently say that 3D printing has revolutionized the world. The author’s passion for additive manufacturing shines through every line, making it an absolute pleasure to read.
I particularly enjoyed the in-depth exploration of various industries, from aerospace and defense to medical and dental, consumer goods, and industrial manufacturing. Each chapter is a masterclass in showcasing the vast potential of 3D printing, its applications, and the benefits it brings to each sector.
One aspect that resonated deeply with me was the emphasis on customization and mass production. As someone who’s spent years navigating the complexities of logistics and supply chain management, I can attest to the fact that traditional manufacturing methods often struggle to keep up with changing consumer demands. 3D printing offers a game-changing solution, enabling companies to produce customized products quickly and efficiently.
The article also highlights the significance of rapid prototyping and design flexibility in industries such as automotive and aerospace. This is something I’ve witnessed firsthand during my time on the road, where manufacturers are constantly striving to improve their products and meet evolving consumer expectations.
As a truck driver, I’ve had the privilege of interacting with various industries, from manufacturing plants to logistics hubs. And let me tell you, 3D printing has already started making waves in these sectors. Companies like Adidas and Chanel are leveraging this technology to create innovative products that showcase the limitless possibilities of additive manufacturing.
In conclusion, this article is a tour de force that showcases the transformative power of 3D printing. It’s an absolute must-read for anyone interested in innovation, technology, or simply staying ahead of the curve. As Eduardo Hunter, I highly recommend it to my fellow truckers and anyone looking to stay informed about the future of manufacturing.
And if you’re considering implementing 3D printing in your organization, I’d be happy to offer some expert advice. After all, as a seasoned truck driver with years of experience navigating complex logistics, I’ve learned a thing or two about making things happen on time and under budget!
Eduardo Hunter, the “seasoned truck driver” who’s also an expert in innovation (I’m not sure if I should be impressed by your multitasking skills or concerned that you might be driving while reading this article).
While I appreciate your enthusiasm for 3D printing, I have to question a few of your points. You claim that traditional manufacturing methods often struggle to keep up with changing consumer demands, but isn’t that exactly what companies like Adidas and Chanel are leveraging 3D printing for? To create innovative products that showcase the technology’s limitless possibilities?
I’m not sure if you’ve driven through any major cities recently, but I’ve seen plenty of factories still churning out mass-produced goods using traditional methods. And let’s be real, Eduardo, your expertise in logistics might be impressive, but have you ever tried to assemble a 3D-printed product with a bunch of loose screws and wires? It’s not exactly rocket science, but it can be a bit of a challenge.
All joking aside, I agree that 3D printing has the potential to revolutionize industries. But let’s not get ahead of ourselves – we need to see more concrete examples of its adoption in various sectors before we can start making sweeping statements about its transformative power.