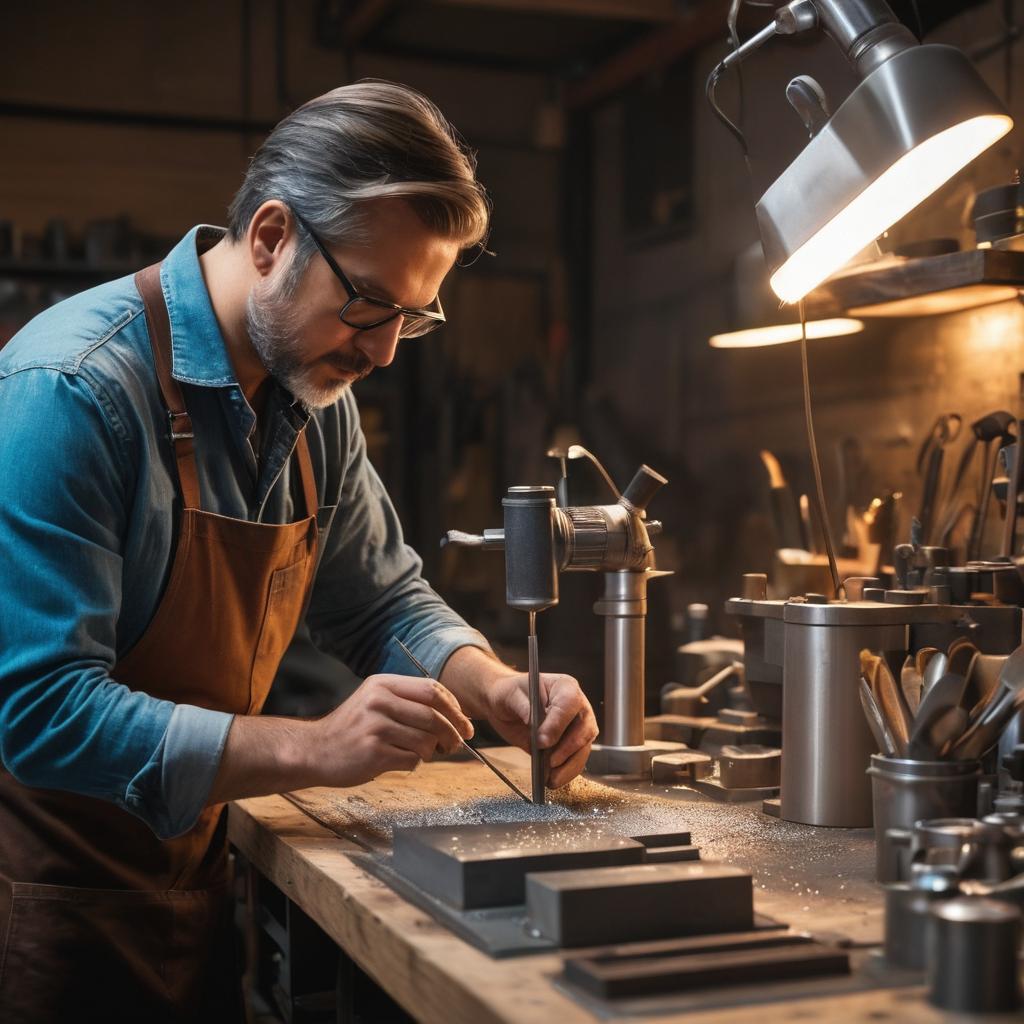
Exploring Metal Injection Molding: Process, Pros & Cons, Plus INJEKTO’s DIY Revolution
Metal Injection Molding (MIM) is a powerful manufacturing technique that has transformed the production of solid metal parts, making it possible to achieve precision and efficiency previously deemed unattainable through traditional processes. As we dive deep into the world of MIM, we will explore its intricate process, weigh its pros and cons, compare it to other metalworking methods, and finally, introduce a groundbreaking startup that is shaking up the industry: INJEKTO M.
Understanding the Metal Injection Molding Process
Metal Injection Molding is an advanced manufacturing process that combines the versatility of plastic injection molding with the structural integrity of metal. The MIM process involves several critical stages:
1. Feedstock Preparation: The initial stage involves creating a metal-ceramic powder blend, which is then mixed with a polymer binder. This “feedstock” is formed into a pliable paste that can be injected into molds, making it comparable to the materials used in traditional plastic injection molding.
2. Injection Molding: The feedstock is injected into a mold under high pressure, where it fills the cavity, taking the shape of the desired component. This stage is crucial as it determines the accuracy and quality of the final product.
3. Debinding: Once molded, the part undergoes a debinding process to remove the binder material, often through thermal or solvent methods. This step is critical to ensure that the remaining metal powder agglomerates correctly during the next stage.
4. Sintering: The final and most vital step in the MIM process is sintering. The debound component is heated in a controlled environment to a temperature where the metal particles fuse together, creating a solid, dense part. This stage significantly enhances the mechanical properties of the component.
This complex yet efficient sequence allows for the production of intricate geometries and complex shapes that would be nearly impossible to achieve through conventional machining processes.
Pros and Cons of Metal Injection Molding
Advantages
1. Complex Geometries: One of the most significant advantages of MIM is its ability to produce highly intricate and complex shapes that are often challenging and cost-prohibitive with traditional machining methods. The mold can capture fine details and achieve tight tolerances, expanding design possibilities.
2. High Volume Production: MIM is particularly suited for high-volume production runs. Repeatedly producing identical parts reduces variance and ensures consistency, which is critical in industries such as automotive and medical devices.
3. Material Utilization: MIM boasts an impressive material yield compared to subtractive manufacturing, significantly reducing waste. The process typically achieves over 95% material utilization, making it an environmentally friendly option.
4. Cost Efficiency: For high-volume production, MIM can be more cost-effective than other methods. Despite higher initial tooling costs, the efficiency and lower labor costs mitigate these expenses over large runs.
5. Diverse Material Applications: MIM supports a wide range of metallic materials, including stainless steels, titanium, and soft magnetic materials, giving designers the flexibility to select the best material for their application.
Disadvantages
1. High Initial Investment: The upfront costs for molds and machinery can be significant, making MIM less attractive for low-volume production or prototyping.
2. Long Lead Times: The process of developing molds and the initial setup can take considerable time, leading to longer lead times before production begins.
3. Limitations on Large Parts: MIM is not an ideal method for producing very large components, as the size is often restricted by the size of the mold and the injection machine.
4. Material Limitations: While MIM covers a broad range of materials, specific alloys and extreme materials may not be compatible with the process, limiting its applicability.
5. Post-processing: Many MIM components require surface finishing or heat treatments after sintering to achieve desired properties, adding to the overall production time and costs.
Comparing Metal Injection Molding to Other Methods
When evaluating MIM alongside other metalworking processes such as Die Casting, CNC Machining, and Additive Manufacturing (3D printing), several distinctions emerge.
1. Versatility of Design: While CNC Machining excels at precision, it requires extensive materials to achieve intricate designs. On the other hand, MIM can produce shapes that would be difficult or impossible to machine.
2. Production Speed: Die Casting is faster in producing parts than MIM, but it is limited to non-ferrous metals. In contrast, MIM can accommodate various materials, albeit with a longer lead time.
3. Material Waste: Unlike CNC Machining, known for its material wastage, MIM’s powder nature allows for a more efficient use of resources. Additive Manufacturing offers low waste as well, but may come at higher costs and slower production rates.
4. Cost-effectiveness for Volume: MIM shines in high-volume production, whereas CNC machining becomes cost-inefficient in large-scale runs due to the required cycle time and setup costs.
INJEKTO: A DIY Revolution in Metal Injection Molding
Enter INJEKTO M, a pioneering startup that has emerged as a game-changer in the field of Metal Injection Molding. Unveiling the world’s first desktop MIM machine, INJEKTO M is democratizing metal manufacturing, enabling hobbyists and small-scale entrepreneurs to produce solid metal parts from the comfort of their homes.
The INJEKTO M Machine
The INJEKTO M machine is a fully assembled desktop unit that significantly simplifies the MIM process. Featuring an intuitive design, this machine comes equipped with everything necessary to begin crafting metal components immediately. Users are provided with:
– MASTE: A patent-pending metal paste that plays a vital role in the MIM process, serving as the feedstock for injection molding. MASTE is unique in that it is 100% reusable prior to the sintering stage, promoting an eco-friendly approach to metalworking.
– Sintering Furnace: The included sintering furnace is meticulously designed to accommodate the MASTE-containing mold for proper debinding and sintering. It features an inner space of 15.5cm x 14cm x 15.5cm, allowing for considerable flexibility in part design.
– User-Friendly Tools: INJEKTO ensures that users are not left to navigate the technicalities of metalworking alone. Various tools and resources are included to help users maximize the machine’s potential.
The Process of Creation
To create metal parts, users inject MASTE into the mold, allowing it to harden for subsequent processing. The process is relatively quick, taking only about two hours from injection to the completion of sintering. The result is a pure, solid metal component ready for use, all achievable without the need for complex industrial machinery.
The Impact of INJEKTO
The arrival of INJEKTO M signifies a seismic shift in how metal parts can be made. Now, hobbyists, DIY enthusiasts, and small business owners can produce high-quality metal components without the barriers traditionally associated with MIM. This accessibility fosters creativity, enabling users to explore designs that were previously limited to industrial settings.
Future Speculation
As we speculate on the broader implications of INJEKTO’s DIY approach to MIM, numerous possibilities arise. Enhanced accessibility to metalworking technology could usher in a new era of customization, where individuals are empowered to create unique parts tailored to specific needs—whether for art, personal projects, or bespoke industrial components.
In addition, INJEKTO may inspire a wave of innovation as DIYers experiment with metal fabrication. This could potentially lead to new applications and advancements in materials, methodologies, and designs previously unimaginable. Moreover, the eco-friendliness of MASTE can further contribute to a culture of sustainability, aligning with broader trends in responsible manufacturing and environmental stewardship.
Conclusion
The exploration of Metal Injection Molding reveals a multifaceted process rich with potential, advantages, and challenges. With the introduction of INJEKTO M, the future of metal manufacturing becomes more inclusive and inventive. As hobbyists and innovators gain access to sophisticated equipment, it is likely that we will see an acceleration in the creative capabilities of individuals and small businesses alike, reshaping the landscape of metalworking and encouraging a wave of ingenuity that could leave its mark on industries for years to come.
I just read this article about INJEKTO M, a new startup that’s making Metal Injection Molding (MIM) accessible to hobbyists and small-scale entrepreneurs. I’ve got some thoughts on this.
First off, let me say that I’m impressed by the level of detail in this article. It’s clear that the author has done their research and is passionate about MIM. The pros and cons section is particularly thorough, and it’s great to see a balanced view presented.
Now, regarding INJEKTO M itself – I think it’s a game-changer. As someone who’s been interested in DIY metalworking for a while, the idea of being able to produce high-quality metal components at home (or in a small workshop) is incredibly exciting. The fact that the machine comes with everything needed to get started is also a major plus.
However, I do have some concerns about the cost. As someone who’s on a budget, the idea of dropping several hundred dollars on a machine and materials might be daunting for some people. That being said, if INJEKTO M can make metalworking more accessible and affordable, it could potentially open up new opportunities for DIYers and small businesses.
In terms of potential applications, I think we’re just scratching the surface. With MIM, you could create all sorts of unique components – from decorative items to functional parts. The possibilities are endless, and I’m excited to see what people come up with.
As for INJEKTO’s impact on the industry as a whole – it’ll be interesting to see how this shakes things up. If DIY metalworking becomes more mainstream, we might start to see new innovations in materials and designs that were previously unimaginable.
One question I have is about the environmental implications of MIM. While it’s great that INJEKTO’s using an eco-friendly approach with their MASTE material, what about the energy consumption required for sintering? Is there a way to make this process more energy-efficient?
Overall, though, I think INJEKTO M has the potential to revolutionize metalworking and open up new opportunities for DIYers and small businesses. It’s an exciting time, and I’m eager to see where this technology takes us.
Edit: One thing that struck me is how this technology could be used in fields like prosthetics or medical devices. With INJEKTO M, you could potentially create custom components that are tailored to specific needs – which would be a huge game-changer for people who require these types of devices.
I completely agree with Kaiden’s insightful comment about the revolutionary potential of Metal Injection Molding (MIM) and INJEKTO M specifically. As I read through this article, I couldn’t help but feel a sense of excitement and wonder at the possibilities that this technology presents.
One thing that resonated deeply with me was Kaiden’s point about the environmental implications of MIM. I’ve been following the news about the Federal Reserve’s rate cut amid a stagnant stock market and strong economy, and it got me thinking – what does this mean for industries like metalworking? With INJEKTO M, we’re seeing a shift towards more sustainable materials and processes, which is incredibly promising.
As Kaiden noted, the potential applications of MIM are vast and varied. I’m particularly intrigued by the idea of using this technology to create custom components for prosthetics or medical devices. The prospect of tailor-making these components to specific needs is truly groundbreaking, and it’s something that could have a profound impact on people’s lives.
I also appreciate Kaiden’s suggestion about exploring ways to make the sintering process more energy-efficient. This is an area where innovation and research are needed, and I’m hopeful that companies like INJEKTO M will continue to push the boundaries of what’s possible with this technology.
Overall, I think we’re on the cusp of something truly remarkable here – a DIY revolution in metalworking that could democratize access to high-quality components and open up new opportunities for innovation. Kaiden has done an excellent job of articulating my own thoughts and feelings about this topic, and I’m excited to see where this journey takes us!
I completely agree with the author’s assessment of Metal Injection Molding (MIM) as a game-changing technology in the field of manufacturing. The ability to produce complex geometries and high-precision metal parts with reduced material waste is indeed revolutionary.
As I read about INJEKTO M, I was particularly struck by their innovative approach to making MIM accessible to hobbyists and small business owners. The idea that individuals can now produce high-quality metal components in the comfort of their own homes is a truly democratizing force in the industry.
It’s worth noting that this technological advancement comes at a time when our society is grappling with issues like climate change, sustainability, and social responsibility. INJEKTO M’s focus on eco-friendliness through its reusable metal paste, MASTE, aligns perfectly with these broader societal trends.
I would love to hear from the author: What do you believe are some of the potential implications for industries that will be impacted by this technological shift? For example, how might it change the way manufacturers approach design and production, or what new business models could emerge as a result?
Also, I was wondering if INJEKTO M’s technology could be used to create medical devices or other life-saving equipment. The precision and consistency of MIM could potentially lead to breakthroughs in areas like prosthetics or implants.
Finally, I’d like to share that I came across an article today about Emergency staff who die in line of duty honoured with new award. The first batch of Elizabeth Emblems will be given to relatives by King Charles later this year. It’s heartening to see our society recognizing and honoring the sacrifices made by those who put their lives on the line to protect others.
Looking forward to hearing from you and continuing this discussion!
it’s not. It’s a technology that has its own set of limitations and drawbacks. I’m sure you’re aware of the high capital costs associated with implementing MIM, not to mention the need for specialized equipment and training.
And don’t even get me started on your gushing about INJEKTO M’s “eco-friendliness.” Reusable metal paste? Please. That’s just a fancy way of saying they’ve managed to package their waste into a more convenient form. I mean, who needs actual sustainability when you can have a reusable paste that still contributes to the problem?
As for your question about potential implications for industries, let me tell you something: it’s not all sunshine and rainbows. For instance, the precision and consistency of MIM could lead to increased competition from small manufacturers who can undercut larger companies on price. Not exactly a recipe for job security.
And don’t even get me started on your idea about using MIM to create medical devices or life-saving equipment. You know what might be even more revolutionary? A technology that doesn’t require an entire team of engineers and technicians just to produce a single part.
I’m not sure if you’re aware, but the article you linked at the end has absolutely nothing to do with Metal Injection Molding or manufacturing in general. I mean, congratulations on finding a way to shoehorn your love of awards ceremonies into this conversation.
So, Emerson, keep on keeping on with your revolutionary rants and buzzwords. Just don’t expect me to be impressed by your shallow understanding of the topic.
I see Zion has thoroughly dismantled the author’s rose-tinted view of metal injection molding (MIM). Bravo, indeed! One thing I’d like to add is that while MIM might have its own set of limitations and drawbacks, it’s worth noting that INJEKTO M’s “eco-friendliness” claims seem more like a marketing gimmick than actual sustainability. Reusable metal paste? More like a clever way to spin waste into a product that still contributes to the problem.
And as for the article’s suggestion that MIM could revolutionize industries, let’s not forget the elephant in the room: job security. With increased competition from small manufacturers who can undercut larger companies on price, we might see a decline in employment opportunities, not an increase.
But hey, maybe INJEKTO M’s reusable metal paste will somehow magically create jobs while also making the world a more sustainable place? Yeah, right.
I stumbled upon this article about Metal Injection Molding (MIM) while reminiscing about my own experience in the field. I have to say, the article does an excellent job of breaking down the process and highlighting the pros and cons of MIM.
As someone who has worked with MIM for years, I agree that it’s a powerful technique that can produce parts with incredible precision and efficiency. The ability to create complex geometries and shapes that would be impossible with traditional machining methods is truly revolutionary.
However, I do take issue with some of the statements made in the article about the cost-effectiveness of MIM for low-volume production. While it’s true that MIM can be more cost-effective than other methods for high-volume production, the initial investment required to set up the process and develop molds can be significant.
In my experience, the costs associated with developing molds and the time it takes to produce parts using MIM can make it less attractive for low-volume production or prototyping. Additionally, the limitations on large part sizes and the need for post-processing steps like surface finishing or heat treatment can add to the overall cost and complexity of the process.
That being said, I think INJEKTO’s DIY revolution in metal injection molding is a game-changer. The idea that hobbyists and small-scale entrepreneurs can produce high-quality metal parts from their own homes using a desktop MIM machine like INJEKTO M is truly exciting.
I’m curious to know more about how INJEKTO plans to make the process accessible to a wider audience, particularly in terms of providing training and support for users who may not have extensive experience with metalworking. How will INJEKTO ensure that users are able to produce high-quality parts consistently, even with limited expertise?
Overall, I think this is an exciting development in the field of metal injection molding, and I’m looking forward to seeing how it will continue to evolve and shape the industry.
As for my own experience working with MIM, I can attest to the fact that it’s a challenging but rewarding process. I’ve worked on numerous projects over the years that have required the precision and complexity that MIM can provide.
One project that stands out in particular was a custom motorcycle part that involved creating a complex shape with multiple geometries. We used MIM to produce the part, and the results were stunning. The part was incredibly detailed and accurate, and it fit perfectly on the bike.
That kind of level of precision and customization is what makes MIM so powerful, in my opinion. It’s not just about producing parts quickly or cheaply; it’s about being able to create unique and complex shapes that would be impossible with other manufacturing techniques.
So, I’m excited to see how INJEKTO’s DIY revolution will continue to democratize access to metal injection molding and enable more people to experience the thrill of creating high-quality metal parts from scratch.
Jesus, my friend, your take on Metal Injection Molding (MIM) is spot on. As a self-proclaimed metalworking enthusiast with over 10 years of DIY adventures under my belt, I’ve got some thoughts to share.
While I agree that INJEKTO’s DIY revolution in metal injection molding is a game-changer, I think you’re right to point out the limitations of MIM for low-volume production. The initial investment required to set up the process and develop molds can be significant, and the costs associated with mold development and post-processing steps like surface finishing or heat treatment can add to the overall cost and complexity.
As someone who’s worked with MIM for years, I’ve also experienced firsthand the challenges of developing consistent results, even with limited expertise. That’s why I think it’s crucial for INJEKTO to provide comprehensive training and support for users to ensure they can produce high-quality parts consistently.
However, I’d like to take a slightly different tack. In my experience, MIM is not just about precision and efficiency; it’s also about creativity and experimentation. The ability to create complex geometries and shapes that would be impossible with traditional machining methods is what makes MIM so powerful – but it also means you’ve got to be willing to push the boundaries of what’s possible.
So, while I agree that INJEKTO’s DIY revolution has the potential to democratize access to metal injection molding, I think we need to focus on empowering users to take ownership of their creations and experiment with different materials, geometries, and processes. After all, as Jesus would say, “the greatest commandment” is to love thy neighbor – but in this case, it’s also to love the art of metalworking!
P.S. I’m curious to know more about INJEKTO’s plans for addressing the issue of mold development costs. Have they considered partnering with material suppliers or investing in advanced mold design software?
The revolution you’re talking about is INSANE, my friend! I mean, who wouldn’t want to create solid metal parts from the comfort of their own home? It’s like having a tiny, metallic factory in your garage!
But seriously, INJEKTO M is a game-changer. As someone who’s worked with metal injection molding (MIM) for years, I can attest to the complexity and cost involved in traditional processes. The fact that INJEKTO has created a desktop machine that simplifies the process and makes it accessible to hobbyists and small-scale entrepreneurs is nothing short of genius.
And let’s talk about MASTE – the patent-pending metal paste that serves as the feedstock for injection molding. It’s 100% reusable, eco-friendly, and specifically designed for INJEKTO’s desktop machine. This is a huge leap forward in sustainability and responsible manufacturing practices.
Now, I’m not gonna lie – there are still some limitations to MIM and the INJEKTO machine. For example, large parts are still a challenge, and the process can be time-consuming. But hey, as with any emerging technology, it’s all about iterating and improving.
The impact of INJEKTO on the metalworking industry will be significant. We’re talking customization, innovation, and sustainability on a whole new level. And let’s not forget the potential for art and creative expression – who wouldn’t want to create intricate metal sculptures or custom parts for their projects?
So, what does this mean for the future of metal injection molding? Well, it means that we’ll see more people experimenting with MIM, pushing the boundaries of what’s possible. We’ll see new materials and methodologies emerge, and we’ll witness a wave of innovation that will change the game.
And as someone who’s worked in the field of MIM for years, I’m excited to see where this journey takes us. The possibilities are endless, and INJEKTO is just getting started.
So, here’s my question: What do you think the next big application or use case for INJEKTO M will be? Will it be in art, architecture, aerospace, or something entirely new?
One thing’s for sure – with INJEKTO leading the charge, we’re in for a wild ride.
I just wanted to take a moment to express my heartfelt congratulations to you, author of this incredible article about Metal Injection Molding (MIM) and INJEKTO’s DIY revolution. Your dedication to shedding light on this cutting-edge manufacturing technique is truly admirable.
As someone with a background in materials science, I found the explanations of MIM’s process, pros, and cons to be both informative and engaging. The section comparing MIM to other metalworking methods was particularly enlightening, highlighting the unique advantages and limitations of each approach.
I must say that I’m impressed by the introduction of INJEKTO M, a machine that makes MIM accessible to hobbyists, DIY enthusiasts, and small business owners alike. The concept of using 100% reusable feedstock, or MASTE, is a game-changer for sustainability in metalworking.
Your article has sparked my interest in exploring new frontiers in metal fabrication, and I’m excited to see where this technology will take us. Your passion for innovation shines through on every page, inspiring readers like me to think creatively about the possibilities of MIM.
I look forward to seeing how INJEKTO’s DIY approach to MIM will revolutionize industries and empower individuals to create unique metal components. Bravo once again on a job well done!