Automation has revolutionized the way industries and manufacturing processes operate, ushering in an era of increased efficiency, precision, and scalability. In production, automation refers to the integration of technology, machinery, and software to perform tasks with minimal human intervention. This transformative approach has not only elevated the speed and quality of production but has also significantly impacted various sectors, ranging from automotive and electronics to pharmaceuticals and food processing.
The concept of automation in production dates back to the Industrial Revolution, with the mechanization of tasks using water and steam power. However, the modern-day automation that we are accustomed to is characterized by advanced technologies such as robotics, artificial intelligence, machine learning, sensors, and control systems. This combination of hardware and software enables not only the execution of repetitive and labor-intensive tasks but also the ability to adapt and optimize processes in real-time.
The key drivers behind the adoption of automation in production are multifaceted. Enhanced productivity and cost reduction are among the primary advantages, as automated systems can operate continuously, eliminating the constraints of human labor hours and reducing the occurrence of errors. This leads to increased throughput, better resource allocation, and ultimately improved profitability for businesses.
Quality control and consistency are equally compelling factors. Automation minimizes the variability introduced by human factors, resulting in products that meet stringent quality standards and exhibit fewer defects. Moreover, automation enables rapid reconfiguration of production lines for different products, allowing manufacturers to swiftly respond to market demands and changing consumer preferences.
Safety considerations also play a crucial role in the rise of automation. Dangerous and physically demanding tasks can be delegated to machines, thereby reducing the risk of workplace accidents and enhancing employee well-being. Humans can be assigned roles that require decision-making, creative thinking, and problem-solving, tasks that leverage their cognitive skills and add significant value to the production process.
However, the integration of automation into production is not without challenges. Initial setup costs, technological complexity, and the need for skilled technicians to operate and maintain automated systems are some of the hurdles that organizations must address. Additionally, the displacement of human workers in certain roles raises questions about the societal impact of automation on employment.
Types of Automation Systems
Automation systems play a pivotal role in transforming industries by streamlining processes, enhancing productivity, and improving overall efficiency. These systems come in various types, each designed to cater to specific tasks, industries, and operational requirements. Here are some of the prominent types of automation systems:
- Fixed or Hard Automation: Fixed automation involves the use of specialized machinery and equipment to perform a specific set of tasks or operations. These systems are designed for high-volume production of identical products. They are characterized by their lack of flexibility – once set up, they are challenging to reconfigure for different products or tasks. Fixed automation is ideal for scenarios where the production process remains constant and consistent, such as assembly lines for products with standardized designs.
- Programmable Automation: Programmable automation systems offer more flexibility compared to fixed automation. They utilize computer-controlled equipment that can be reprogrammed to perform different tasks or processes. This type of automation is suitable for situations where product variations are relatively frequent, allowing manufacturers to adapt their processes without completely overhauling the production line. Programmable automation finds application in industries where product designs change regularly or customization is required.
- Flexible or Soft Automation: Flexible automation systems are designed to handle a variety of tasks and processes within a certain range. These systems use robotics and advanced control mechanisms to efficiently switch between different tasks. They excel in environments where there is a need for frequent product changeovers or where production volumes vary significantly. Flexible automation strikes a balance between the specificity of fixed automation and the adaptability of programmable automation.
- Industrial Robotics: Industrial robots are automated machines that can perform a wide range of tasks with precision, speed, and accuracy. They are widely used in manufacturing, assembly, and material handling processes. Industrial robots can be articulated arms, cartesian robots, delta robots, or SCARA robots, each designed for specific tasks. Advances in robotics technology, including sensors and machine learning, have enabled robots to perform more complex and delicate tasks alongside humans.
- CNC Machines: Computer Numerical Control (CNC) machines are widely used in industries such as machining, woodworking, and metalworking. These machines are controlled by computers to execute precise and intricate operations on raw materials. CNC machines offer high levels of accuracy and repeatability, making them essential for producing intricate components with minimal human intervention.
- Automated Assembly Systems: Automated assembly systems involve the integration of various components and parts to create a finished product. These systems use robotics, conveyor belts, and advanced sensors to ensure proper alignment, attachment, and quality control during the assembly process. They are commonly used in industries such as automotive, electronics, and consumer goods manufacturing.
- Process Automation: Process automation focuses on controlling and optimizing complex processes in industries like chemical, pharmaceutical, and food production. It involves the use of control systems, sensors, and software to monitor and adjust variables such as temperature, pressure, and flow rates. Process automation enhances efficiency, consistency, and safety in industries where precise control is paramount.
- Home and Service Automation: Automation is not limited to industrial settings; it has also made its way into homes and service sectors. Home automation involves controlling household appliances, lighting, heating, and security systems through smart devices. Service automation encompasses customer service interactions, chatbots, and automated responses, improving the efficiency of service delivery.
Each type of automation system offers unique benefits and challenges, and the choice of system depends on factors such as production volume, product variability, and the level of human interaction required. As technology continues to advance, these automation systems are likely to become even more sophisticated, playing an increasingly integral role in shaping the future of various industries.
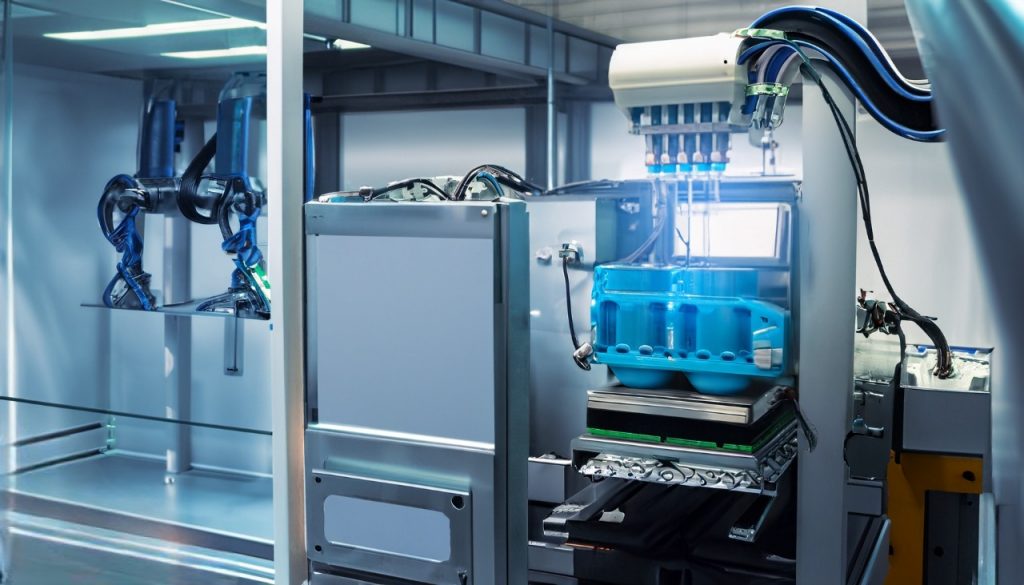
Benefits of Automation in Production
Automation has emerged as a transformative force that reshapes industries and production processes, offering a multitude of benefits that impact efficiency, quality, and overall business performance. From improved productivity to enhanced safety, the advantages of automation are far-reaching and have a significant impact on various aspects of production. Here are some key benefits of automation in production:
- Increased Productivity: One of the primary advantages of automation is the substantial increase in productivity. Automated systems can work continuously without breaks, reducing downtime and maximizing the utilization of resources. They can perform tasks at a faster pace than human workers, leading to higher output and shorter production cycles. This boost in productivity translates to increased production capacity and the ability to meet growing demand.
- Enhanced Quality and Consistency: Automation systems excel at maintaining consistent quality in production processes. By eliminating human errors and minimizing variations, automated systems ensure that products meet exact specifications and stringent quality standards. This consistency reduces the likelihood of defects, rejects, and rework, resulting in higher-quality products and improved customer satisfaction.
- Improved Efficiency and Resource Utilization: Automated systems optimize resource utilization by precisely controlling factors such as material usage, energy consumption, and production flow. This efficiency minimizes waste and reduces the consumption of raw materials, energy, and other resources, leading to cost savings and more sustainable production practices.
- Reduced Labor Costs: Automation significantly reduces the need for manual labor, especially for repetitive and labor-intensive tasks. While skilled technicians are required to operate and maintain automated systems, the overall labor costs can be reduced, particularly in tasks where human involvement is resource-intensive.
- Enhanced Safety: Automation contributes to a safer work environment by handling hazardous and physically demanding tasks. This reduces the risk of workplace accidents and injuries, creating a safer atmosphere for human workers. Dangerous tasks such as heavy lifting, exposure to toxic substances, or working in extreme conditions can be assigned to automated systems.
- 24/7 Operation: Automated systems can operate around the clock without the need for breaks or shifts. This continuous operation ensures that production processes can be maintained non-stop, resulting in higher overall output and faster response times to market demands.
- Flexibility and Adaptability: Certain types of automation systems, such as flexible automation, allow for rapid reconfiguration and adaptation to changing production needs. This flexibility enables manufacturers to respond quickly to shifts in consumer demand, product variations, and market trends, thus maintaining a competitive edge.
- Data Collection and Analysis: Automation systems generate vast amounts of data related to production processes, product quality, and equipment performance. This data can be collected, analyzed, and utilized to identify opportunities for process improvement, predictive maintenance, and overall optimization of production operations.
- Scalability: As businesses grow, automation can be easily scaled to accommodate higher production volumes. This scalability ensures that production capabilities can expand without significant investments in additional human resources.
- Innovation and R&D: With routine tasks delegated to automation, human workers can focus on innovation, research, and development. This allows companies to invest in creating new products, improving existing ones, and exploring novel production techniques.
Automation’s benefits extend beyond immediate efficiency gains, influencing various aspects of production and business operations. As technology continues to advance, automation’s role in shaping the future of industries becomes increasingly critical, offering companies the tools to remain competitive, agile, and responsive to the ever-evolving demands of the market.
Role of Robotics in Automated Production
Robotics has emerged as a cornerstone of modern automated production processes, revolutionizing industries across the globe. These intelligent machines, equipped with sensors, actuators, and sophisticated control systems, play a pivotal role in enhancing efficiency, precision, and flexibility within manufacturing environments. The integration of robotics in automated production brings about a range of benefits that shape the way products are designed, manufactured, and delivered to consumers. Here’s an exploration of the significant role that robotics plays in automated production:
- Increased Productivity and Throughput: Robots are designed to work tirelessly and consistently, 24/7, without the need for breaks or shifts. This uninterrupted operation leads to a substantial increase in production throughput. Robots can perform tasks at a faster pace than human workers, thereby reducing cycle times and boosting overall productivity.
- Precision and Accuracy: Precision is a hallmark of robotics. These machines can perform intricate and complex tasks with a high degree of accuracy, making them invaluable for applications that require precise measurements, alignments, and assembly. This level of precision contributes to higher product quality and reduced error rates.
- Labor Savings and Cost Efficiency: Robots can replace human workers in performing repetitive, monotonous, and physically demanding tasks. This reduction in manual labor requirements leads to significant cost savings over time, as companies can allocate their human workforce to more strategic and creative tasks.
- Flexible Automation: Modern robotic systems are designed for flexibility, capable of being reprogrammed or reconfigured to perform different tasks or handle various product variants. This adaptability is especially valuable in industries with rapidly changing product designs or demand patterns.
- Complex and Hazardous Tasks: Robots are well-suited for tasks that involve hazardous conditions, such as working in extreme temperatures, toxic environments, or spaces that are unsafe for humans. By delegating these tasks to robots, companies can improve workplace safety and mitigate human health risks.
- Consistency and Quality Control: Robots excel at maintaining consistency in repetitive tasks, leading to uniform product quality. Their ability to perform tasks with minimal variability contributes to a reduction in defects, rejects, and rework, ultimately improving overall product quality.
- Collaborative Workspaces: Collaborative robots, or cobots, are designed to work alongside humans in shared workspaces. These robots are equipped with sensors that allow them to detect human presence and respond accordingly, enabling them to assist with tasks that require human-robot collaboration.
- Data Generation and Analysis: Robots generate vast amounts of data during their operations, including information related to performance, errors, and production metrics. This data can be collected, analyzed, and used to optimize processes, predict maintenance needs, and identify areas for improvement.
- Innovation and Customization: By automating routine and labor-intensive tasks, robotics frees up human workers to focus on innovation, research, and development. This empowers companies to invest in creating innovative products, exploring new technologies, and responding to market trends.
- Scalability: Robotic systems can be easily scaled to accommodate changing production volumes, ensuring that companies can meet fluctuating demand without significant adjustments to their workforce.
- Market Competitiveness: Adopting robotics in automated production can provide a competitive edge by improving efficiency, product quality, and responsiveness to market demands. Companies that leverage robotics can offer better products at competitive prices, establishing themselves as industry leaders.
Robotics plays a pivotal role in shaping the landscape of automated production. Its versatility, precision, and adaptability contribute to increased productivity, enhanced quality, and the ability to respond to the dynamic demands of modern industries. As robotics technology continues to evolve, its impact on production processes is expected to grow, offering new possibilities for innovation and efficiency across various sectors.
Automation Technologies and Tools
Automation technologies and tools have become the driving force behind the transformation of industries, revolutionizing production processes, enhancing efficiency, and enabling businesses to remain competitive in an ever-evolving market. These technologies encompass a wide range of tools, software, hardware, and systems that work together to streamline operations, reduce manual intervention, and optimize overall performance. Here’s an overview of some key automation technologies and tools that are shaping the landscape of modern production:
- Industrial Robotics: Industrial robots are perhaps the most recognizable form of automation technology. These versatile machines are equipped with arms, actuators, and sensors that allow them to perform a variety of tasks with precision and consistency. Whether it’s assembly, welding, material handling, or packaging, industrial robots play a critical role in automating processes that require accuracy and efficiency.
- Programmable Logic Controllers (PLCs): PLCs are specialized computers used to control and automate electromechanical processes in manufacturing environments. They monitor input signals, make decisions based on programmed logic, and control output devices. PLCs are ideal for tasks that involve controlling machinery, processes, and production lines.
- Human-Machine Interfaces (HMIs): HMIs are user interfaces that allow human operators to interact with and monitor automated systems. They provide real-time information on system status, process variables, and alarms. HMIs enhance communication and enable operators to make informed decisions to ensure smooth production operations.
- Sensors and Actuators: Sensors play a vital role in automation by capturing real-time data from the production environment. These sensors can detect factors such as temperature, pressure, humidity, motion, and more. Actuators, on the other hand, are used to initiate actions based on sensor inputs. Together, sensors and actuators enable automation systems to respond to changes and adjust processes accordingly.
- Machine Vision Systems: Machine vision systems use cameras and image processing software to analyze visual information and make decisions based on what they “see.” These systems are used for quality control, product inspection, and defect detection in manufacturing processes.
- Computer Numerical Control (CNC) Machines: CNC machines are automated tools that use computer programming to control the movement of machine tools and equipment. They are commonly used in machining processes like milling, turning, and drilling to produce precise and intricate parts.
- Automated Guided Vehicles (AGVs) and Drones: AGVs are mobile robots that navigate predefined routes to transport materials or products within a facility. Drones, in the context of automation, can be used for tasks such as inventory management, surveillance, and even product delivery.
- Process Control Systems: Process control systems involve the use of sensors, controllers, and software to manage and optimize complex manufacturing processes. These systems ensure that variables such as temperature, pressure, and flow rates are maintained within specified ranges for efficient production.
- Artificial Intelligence (AI) and Machine Learning (ML): AI and ML technologies are being increasingly integrated into automation systems to enable predictive maintenance, anomaly detection, and optimization. These technologies analyze large datasets to identify patterns, make predictions, and adapt processes in real-time.
- Robotic Process Automation (RPA): RPA involves the use of software robots to automate repetitive and rule-based tasks that were traditionally performed by humans. RPA is commonly used in administrative processes, data entry, and data manipulation.
- Simulation and Digital Twins: Simulation tools and digital twins allow manufacturers to create virtual replicas of physical systems. These tools enable testing, optimization, and predictive analysis before implementing changes in the real production environment.
- Cloud Computing and IoT Integration: Cloud computing and the Internet of Things (IoT) facilitate connectivity and data exchange between devices, sensors, and systems. This connectivity enables centralized monitoring, remote control, and data analysis, leading to more informed decision-making.
As industries continue to embrace automation, the synergy of these technologies and tools drives innovation and efficiency, propelling businesses toward a more streamlined and agile future. The integration of these automation technologies empowers companies to adapt to changing market demands, improve product quality, and stay at the forefront of their respective industries.
Conclusion
The role of automation in production is nothing short of transformative, reshaping industries, redefining processes, and propelling businesses into a new era of efficiency and innovation. From the assembly lines of yesteryears to the sophisticated robotics and advanced software solutions of today, automation has evolved into a dynamic force that optimizes production, enhances quality, and shapes the future of various sectors.
Automation’s impact is far-reaching. It has revolutionized the way products are manufactured, introducing precision and consistency that were previously unattainable. The integration of technologies such as industrial robotics, sensors, artificial intelligence, and machine learning has led to production processes that are not only faster but also adaptable to changing demands and product variations. This adaptability ensures that industries remain agile in the face of evolving markets and customer preferences.
The benefits of automation span the spectrum of production-related concerns. It has elevated productivity to new heights, enabling companies to meet growing demands while reducing costs through optimized resource utilization and reduced manual labor requirements. Moreover, automation contributes to safer working environments by taking on hazardous tasks and allowing human workers to focus on tasks that require creativity, problem-solving, and innovation.
Quality control has been revolutionized by automation’s ability to maintain consistency and accuracy in tasks that were once prone to human error. This leads to products of superior quality and fewer defects, ultimately translating to increased customer satisfaction and loyalty.
Yet, the journey toward full automation is not without challenges. Initial costs, technological complexity, workforce adaptation, and ethical considerations related to job displacement require careful consideration. Striking the right balance between automation and human intervention is a delicate endeavor that calls for strategic planning and a long-term perspective.
Automation in production has ushered in an era of unprecedented possibilities. It has redefined what is achievable in terms of speed, precision, flexibility, and cost-effectiveness. As automation technologies continue to advance, the potential for greater integration, optimization, and innovation becomes even more promising. Embracing automation not only transforms the way industries operate but also ensures that businesses remain competitive and relevant in a rapidly evolving global landscape. The symbiotic relationship between human ingenuity and automated efficiency is poised to shape the future of production, promising a world of smarter, more sustainable, and highly responsive industries.