Industrial automation systems have revolutionized the way industries operate and produce goods. With the integration of advanced technologies, these systems have significantly enhanced efficiency, precision, and flexibility in various manufacturing and production processes. This introduction aims to provide an overview of industrial automation systems, their components, benefits, and the impact they have on modern industrial practices.
Defining Industrial Automation: Industrial automation refers to the utilization of control systems, machinery, and information technologies to streamline and optimize industrial processes, reducing the need for direct human intervention. It involves the integration of various hardware and software components to control and monitor complex tasks, ranging from material handling and assembly to quality control and data analysis.
Components of Industrial Automation Systems:
- Sensors and Actuators: These devices are the sensory organs and muscles of automation systems. Sensors gather data from the environment, while actuators perform actions based on the received data. They enable the system to perceive and interact with its surroundings.
- Programmable Logic Controllers (PLCs): PLCs are rugged industrial computers designed to control machinery and processes. They can be programmed to execute specific tasks, follow logic sequences, and respond to input signals from sensors.
- Human-Machine Interface (HMI): The HMI provides a visual and interactive platform for operators and engineers to monitor the system, receive real-time data, and input commands. It simplifies the communication between humans and machines.
- Supervisory Control and Data Acquisition (SCADA): SCADA systems oversee and manage industrial processes on a larger scale. They gather and display real-time data, control remote equipment, and enable operators to make informed decisions.
- Distributed Control Systems (DCS): DCSs are specialized systems commonly used in large-scale industrial processes such as power generation and chemical production. They manage complex processes across various locations and integrate control elements.
- Robotics: Industrial robots automate tasks that require precision, repetition, and speed. They are employed in tasks such as welding, assembly, material handling, and even complex surgeries in the medical field.
Benefits of Industrial Automation:
- Improved Efficiency: Automation reduces the chances of human error, increases production speed, and ensures consistent quality, leading to higher overall efficiency.
- Enhanced Safety: Dangerous and repetitive tasks can be assigned to robots, ensuring the safety of human workers and reducing workplace accidents.
- Higher Precision: Automation systems can achieve levels of precision that might be unattainable for humans, leading to higher product quality and reduced waste.
- Flexibility and Adaptability: Modern automation systems can be easily reconfigured and programmed to adapt to changing production requirements, allowing for faster response to market demands.
- Data Collection and Analysis: Automation systems generate vast amounts of data, which can be analyzed to identify trends, optimize processes, and make informed business decisions.
- Cost Savings: While initial implementation costs can be significant, automation often leads to long-term cost savings through reduced labor costs, increased production, and decreased downtime.
Impact on Modern Industries: The integration of industrial automation systems has transformed industries such as manufacturing, automotive, aerospace, pharmaceuticals, and logistics. It has allowed these sectors to stay competitive in a rapidly evolving global market by improving efficiency, product quality, and innovation.
In conclusion, industrial automation systems represent a pivotal advancement in modern industrial practices. By combining cutting-edge technology with intelligent control systems, these systems optimize processes, enhance productivity, and pave the way for a more efficient and competitive industrial landscape.
Components of Industrial Automation Systems
Industrial automation systems are composed of various interconnected components that work together to control and manage industrial processes. These components play distinct roles in ensuring the automation of tasks, efficient data handling, and seamless communication within the system. Here are the key components of industrial automation systems:
- Sensors and Actuators: Sensors are devices that detect and gather data from the environment. They measure physical parameters such as temperature, pressure, humidity, proximity, and more. Actuators, on the other hand, perform physical actions based on the data received from sensors. For example, actuators can control valves, motors, pumps, and other devices. These components are essential for providing the system with real-time information and enabling it to respond to changes in the environment.
- Programmable Logic Controllers (PLCs): PLCs are industrial computers designed to control machinery and processes. They are programmable devices that execute specific tasks and automation sequences based on the input they receive from sensors and other sources. PLCs can process digital and analog signals, making decisions and sending commands to actuators accordingly. They play a central role in automating processes and ensuring that tasks are performed accurately and efficiently.
- Human-Machine Interface (HMI): The HMI is the user-friendly interface that allows operators and engineers to interact with the automation system. It provides visual representations of the industrial processes, real-time data monitoring, and the ability to input commands. HMIs can be in the form of touchscreens, monitors, or other graphical displays. A well-designed HMI enhances the operator’s ability to monitor and control the system effectively.
- Supervisory Control and Data Acquisition (SCADA): SCADA systems are used to monitor, control, and manage industrial processes on a larger scale. They collect data from sensors, PLCs, and other devices, and present it in a comprehensible format to operators and supervisors. SCADA systems enable remote monitoring and control of various components and processes across different locations. They often include alarms, trend analysis, and historical data logging features.
- Distributed Control Systems (DCS): DCSs are specialized systems designed for managing complex industrial processes in industries such as power generation, oil and gas, and chemical manufacturing. Unlike PLCs, DCSs are more suitable for processes that span larger areas and involve multiple control loops. DCSs integrate control elements, sensors, and actuators to ensure precise and coordinated control of various aspects of the process.
- Robotics and Motion Control: Robotics plays a vital role in industrial automation, especially in tasks that require precision, speed, and repeatability. Industrial robots are equipped with their own control systems and programming interfaces. Motion control systems, on the other hand, manage the movement of motors and actuators with high precision, enabling accurate positioning and motion sequences.
- Communication Networks: Automation components communicate with each other through various communication protocols and networks. These networks facilitate the exchange of data and commands between sensors, actuators, PLCs, HMIs, SCADA systems, and other devices. Common industrial communication protocols include Ethernet, Profibus, Modbus, and CAN bus.
- Safety Systems: Industrial automation systems often include safety components to ensure the protection of workers and equipment. Safety sensors, emergency stop buttons, and safety interlocks are integrated into the automation system to detect unsafe conditions and halt processes if necessary.
By combining these components, industrial automation systems create a cohesive and efficient environment where processes can be controlled, monitored, and optimized to enhance productivity, safety, and overall operational excellence.
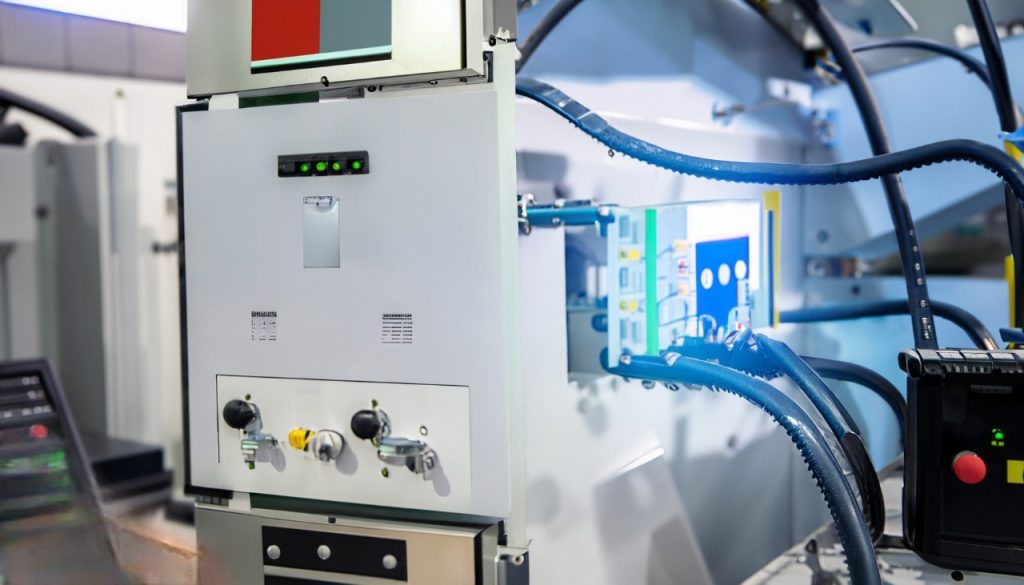
Types of Industrial Automation Systems
Industrial automation systems encompass a wide range of technologies and approaches designed to streamline and optimize various industrial processes. These systems are categorized into different types based on their scope, complexity, and specific applications. Here are some of the main types of industrial automation systems:
- Fixed or Hard Automation: Fixed automation, also known as hard automation, is characterized by the use of specialized machinery and equipment designed to perform a specific task or a set of tasks with little or no variation. These systems are highly efficient for high-volume production of standardized products. Once set up, they require minimal human intervention and are optimized for speed, accuracy, and repeatability. Examples include assembly lines in automotive manufacturing and certain types of food processing.
- Flexible or Soft Automation: Flexible automation systems are designed to handle tasks that require some degree of variability or customization. These systems can be reconfigured or reprogrammed to adapt to different product variations and process changes. Flexible automation is particularly useful in industries where product designs change frequently, allowing for quicker transitions between different product lines. It strikes a balance between the efficiency of hard automation and the adaptability of manual labor.
- Programmable Logic Controllers (PLC) Automation: PLC automation systems involve the use of programmable logic controllers to control machinery and processes. These systems are widely used in manufacturing and industrial facilities to automate tasks such as material handling, machine control, and assembly. PLCs can be programmed to execute specific logic sequences and respond to sensor input, making them versatile tools for a variety of applications.
- Robotics and Robotic Automation: Robotic automation involves the use of industrial robots to perform tasks that require precision, speed, and repeatability. These robots can handle tasks like welding, painting, assembly, and material handling. Robotic systems are programmed to follow specific paths and perform sequences of actions, making them ideal for complex and repetitive tasks. Collaborative robots (cobots) are a subset of robotic automation that work alongside human operators, enhancing efficiency and safety.
- Process Automation: Process automation focuses on controlling and optimizing continuous industrial processes such as chemical production, oil refining, and power generation. These systems involve the use of sensors, controllers, and actuators to monitor and adjust variables like temperature, pressure, flow rate, and chemical composition. Distributed Control Systems (DCS) and SCADA systems are commonly used in process automation to manage and regulate these complex processes.
- Information Technology (IT) and Operational Technology (OT) Integration: With the rise of Industry 4.0 and the Industrial Internet of Things (IIoT), there’s a growing trend of integrating IT and OT systems. This involves connecting industrial machines, sensors, and devices to the internet and centralizing data in cloud-based platforms. This integration enables real-time data analysis, predictive maintenance, and remote monitoring, ultimately leading to increased efficiency and data-driven decision-making.
- Batch Automation: Batch automation systems are used in industries that produce goods in batches, such as pharmaceuticals and food processing. These systems automate the steps involved in batch production, from ingredient mixing and processing to packaging and labeling. Batch automation ensures consistency, traceability, and compliance with quality standards.
- Motion Control Systems: Motion control systems are responsible for precisely controlling the movement of motors, actuators, and robotic arms. These systems are essential for tasks that involve accurate positioning, such as CNC machining, 3D printing, and pick-and-place operations.
These different types of industrial automation systems cater to the diverse needs of industries, offering solutions to improve efficiency, quality, and productivity while reducing human intervention and error. The choice of the appropriate type depends on factors like the nature of the tasks, production volume, customization requirements, and the level of integration with other systems.
Industrial Communication Networks
Industrial communication networks are essential components of modern industrial automation systems, enabling seamless data exchange, control, and coordination among various devices, sensors, controllers, and other elements within an industrial environment. These networks play a critical role in ensuring efficient and reliable communication, which is vital for optimizing processes, improving productivity, and making informed decisions. Here are the key aspects of industrial communication networks:
Types of Industrial Communication Networks:
- Ethernet-Based Networks: Ethernet is widely used in industrial settings due to its high data transmission rates, scalability, and compatibility with standard IT networks. Industrial Ethernet protocols such as Ethernet/IP, PROFINET, and Modbus TCP are used to connect devices like PLCs, HMIs, robots, and sensors. Ethernet-based networks are suitable for applications requiring real-time control, large data volumes, and integration with enterprise systems.
- Fieldbus Networks: Fieldbus networks are older communication protocols used to connect industrial devices and sensors in a local area. Examples include PROFIBUS, DeviceNet, and AS-Interface. Fieldbus networks are cost-effective for applications with moderate data requirements and slower update rates, but they may not be as suitable for high-speed or complex systems.
- Wireless Networks: Wireless communication technologies are gaining prominence in industrial automation due to their flexibility and mobility. Wi-Fi, Bluetooth, Zigbee, and cellular networks are used to connect devices in areas where wired connections are challenging or impractical. Wireless networks are often employed for remote monitoring, mobile robots, and IoT devices.
- Industrial Internet of Things (IIoT) Networks: IIoT networks enable the integration of sensors, devices, and machines into a unified ecosystem. Protocols like MQTT and CoAP are used for lightweight, efficient communication between edge devices and cloud platforms. IIoT networks are crucial for data collection, analysis, predictive maintenance, and remote monitoring.
- Safety Networks: Safety networks ensure the reliable and safe operation of industrial processes. They use protocols like PROFIsafe and Safety over EtherCAT to implement safety functions such as emergency stops, safety interlocks, and protective device monitoring. Safety networks have strict requirements for reliability and quick response times.
Key Features and Considerations:
- Deterministic Communication: Many industrial applications demand deterministic communication, where data transmission occurs within predictable timeframes. This is crucial for real-time control and coordination of processes. Industrial Ethernet protocols often offer deterministic capabilities through features like time-sensitive networking (TSN).
- Scalability and Flexibility: Communication networks should be scalable to accommodate changing requirements and additions to the system. Network architectures should allow easy expansion without disrupting ongoing operations.
- Redundancy and Reliability: Industrial environments require high network reliability. Redundancy mechanisms like ring topologies, redundant paths, and hot-swappable components are used to ensure continuous operation, even in the event of network failures.
- Security: Industrial networks must address cybersecurity concerns to prevent unauthorized access, data breaches, and potential threats to operations. Network segmentation, firewalls, and encryption are employed to enhance security.
- Compatibility and Interoperability: Devices from different manufacturers and generations should be able to communicate seamlessly. Standardized communication protocols and open-source solutions facilitate interoperability.
- Latency and Jitter: For real-time control, minimizing communication latency (delay) and jitter (variation in delay) is crucial. Network configurations and protocols should be optimized to reduce latency and jitter.
Industrial communication networks are the backbone of modern automation systems, enabling the exchange of information and control signals that drive efficient, safe, and productive industrial processes. Selecting the appropriate network type and configuring it effectively are critical steps in designing robust and high-performance industrial automation solutions.
Control Systems and Strategies
Control systems and strategies are fundamental to the functioning of industrial automation, ensuring that processes, machines, and devices operate efficiently, reliably, and with precision. These systems employ various techniques and methods to regulate variables, maintain desired conditions, and achieve specific performance goals. Here’s an overview of control systems, their types, and common strategies:
Control System Basics:
A control system is a set of devices, components, and algorithms that work together to manage the behavior of a system or process. The primary goal is to regulate output variables based on input and feedback, ensuring that the system’s performance aligns with desired targets.
Types of Control Systems:
- Open-Loop Control: Open-loop control involves setting a predetermined control action without feedback. The control input remains constant regardless of variations in the system’s output. While simple and fast, open-loop control is less accurate and can’t adapt to changing conditions.
- Closed-Loop Control (Feedback Control): Closed-loop control utilizes feedback from the system’s output to adjust the control action. The actual output is compared to a desired setpoint, and corrections are made accordingly. Closed-loop control is more accurate and capable of responding to disturbances and changes in the system.
Control Strategies:
- Proportional-Integral-Derivative (PID) Control: PID control is a widely used strategy that adjusts the control output based on three components: proportional (P) for immediate error correction, integral (I) for accumulated error correction, and derivative (D) for anticipating future error trends. PID control is versatile and effective for various applications.
- On-Off Control: On-off control (also known as bang-bang control) switches the control action between two states: on and off. It’s used for systems with simple requirements where precise control isn’t necessary. However, it can lead to oscillations around the setpoint.
- Feedforward Control: Feedforward control anticipates disturbances and adjusts the control input preemptively. It doesn’t rely on feedback but rather on the prediction of disturbances using models or sensor measurements.
- Cascade Control: Cascade control involves using multiple control loops to control a single process. The output of one loop controls the setpoint of another, allowing for more precise control of complex systems with multiple variables.
- Model Predictive Control (MPC): MPC uses a dynamic model of the system to predict its behavior over a specified time horizon. It optimizes control actions to minimize deviations from the desired trajectory, making it suitable for processes with constraints and complex dynamics.
- Adaptive Control: Adaptive control adjusts control parameters based on changes in the system’s behavior or operating conditions. It’s used when system dynamics vary or are uncertain.
- Fuzzy Logic Control: Fuzzy logic control uses linguistic rules and reasoning to handle imprecise or uncertain information. It’s particularly useful when dealing with systems that involve human judgment or linguistic terms.
- Neural Network Control: Neural networks can learn complex relationships between inputs and outputs, making them suitable for nonlinear systems with intricate dynamics.
Selecting Control Strategies:
The choice of control strategy depends on factors like system complexity, required accuracy, response time, disturbance sensitivity, and available information. In many cases, a combination of strategies might be employed to achieve optimal performance.
Control systems and strategies are at the core of industrial automation, enabling the achievement of desired outcomes while maintaining stability, efficiency, and safety in various industrial processes and applications.
Applications of Industrial Automation Systems
Industrial automation systems find applications across diverse industries, revolutionizing manufacturing processes, improving product quality, increasing efficiency, and enhancing safety. These systems integrate various technologies to streamline operations and achieve higher levels of precision, productivity, and control. Here are some notable applications of industrial automation systems:
- Manufacturing and Assembly: Automation has profoundly impacted manufacturing and assembly processes. It’s used for tasks like material handling, part sorting, assembly line automation, and quality control. Robots and machines can perform repetitive and intricate tasks with precision, leading to consistent product quality and reduced production times.
- Automotive Industry: Automotive manufacturing relies heavily on automation for tasks such as welding, painting, assembly, and inspection. Robots play a critical role in welding car frames, installing components, and testing systems, ensuring efficient production and high-quality vehicles.
- Food and Beverage Processing: Automation systems are used in food and beverage production for tasks like packaging, sorting, labeling, and quality control. These systems improve hygiene, reduce waste, and maintain consistency in food processing operations.
- Pharmaceuticals and Life Sciences: The pharmaceutical industry benefits from automation in drug discovery, testing, and manufacturing. Automated systems ensure accurate dosage formulation, precise mixing, and stringent quality control to meet regulatory standards.
- Chemical Industry: Industrial automation is crucial in the chemical sector for handling hazardous substances, controlling reactions, and managing complex processes. Automation improves safety, efficiency, and consistency in chemical manufacturing.
- Energy and Utilities: Automation systems are vital in power generation, distribution, and monitoring. Control systems manage processes in power plants, ensuring optimal energy production and distribution while adhering to safety protocols.
- Logistics and Warehousing: Automated systems in logistics include conveyor systems, robotic picking and packing, and automated guided vehicles (AGVs) for material handling. These systems optimize warehouse operations, reduce errors, and speed up order fulfillment.
- Aerospace and Aviation: Aerospace manufacturing relies on automation for tasks like precision machining, composite material layup, and quality inspection. Automation ensures the highest standards are met in building aircraft components.
- Mining and Extractive Industries: Automation systems improve safety and efficiency in mining operations. Remote-controlled equipment and autonomous vehicles are used for tasks in hazardous environments, reducing the risk to human workers.
- Water and Wastewater Treatment: Automation plays a significant role in managing water treatment processes, optimizing chemical dosing, and monitoring water quality. It ensures the delivery of safe drinking water and efficient wastewater treatment.
- Medical Device Manufacturing: Automation is crucial in producing medical devices with high precision and consistency. It ensures the sterile manufacturing environment required for medical products and devices.
- Textile Industry: Automation systems are employed in textile manufacturing for tasks like spinning, weaving, and dyeing. These systems improve efficiency, quality, and production rates in the textile sector.
- Printing and Packaging: Automation is used in printing and packaging industries for processes such as label application, packaging assembly, and quality inspection. It increases production speed and accuracy while minimizing waste.
These applications demonstrate the transformative impact of industrial automation systems across various sectors. As technology continues to advance, the scope and possibilities for automation will likely expand, leading to further optimization and innovation in industries around the world.
Conclusion
Industrial automation systems stand as the cornerstone of modern industrialization, redefining the way industries operate, produce, and innovate. These systems combine advanced technologies, intelligent control, and precise execution to optimize processes, enhance productivity, and ensure safety across a wide range of sectors. From manufacturing and automotive to pharmaceuticals and logistics, the applications of industrial automation are extensive and transformative.
The components of industrial automation systems, including sensors, actuators, controllers, and communication networks, work in harmony to create efficient and interconnected ecosystems. These systems not only reduce the reliance on human intervention but also elevate the quality of products, increase operational speed, and minimize errors, leading to improved profitability and competitiveness.
As industries embrace Industry 4.0 principles and the Industrial Internet of Things (IIoT), industrial automation systems continue to evolve. The integration of data analytics, artificial intelligence, and cloud-based solutions further amplifies their impact, enabling predictive maintenance, remote monitoring, and real-time decision-making.
However, the adoption of industrial automation is not without challenges. Integrating these systems requires expertise, investment, and adaptability to changing technologies. Furthermore, considerations for cybersecurity, ethical implications, and the potential displacement of certain jobs need to be addressed responsibly.
In a rapidly evolving global landscape, industrial automation stands as a testament to human innovation and adaptability. Its transformative capabilities not only drive operational efficiency but also empower industries to meet the demands of the future. As technology continues to push boundaries, industrial automation systems are poised to shape industries, economies, and societies for years to come.
Recent Comments