In the rapidly evolving landscape of industrial automation, Programmable Logic Controllers (PLCs) have emerged as indispensable tools for controlling and monitoring complex processes across various sectors. PLCs play a pivotal role in ensuring the efficiency, reliability, and safety of manufacturing and industrial operations. However, like any technology, PLCs are subject to wear and tear, environmental factors, and technical glitches that can lead to downtime, production losses, and compromised safety. This underscores the critical importance of implementing a comprehensive preventive maintenance and troubleshooting strategy for PLCs.
Preventive maintenance involves a proactive approach aimed at preventing potential failures before they occur. It encompasses a range of scheduled tasks, inspections, and checks that help identify and address issues in PLCs before they escalate into major problems. By implementing a well-structured preventive maintenance plan, industries can significantly enhance the lifespan of their PLC systems, optimize operational efficiency, and reduce the risk of unexpected breakdowns.
However, despite the best preventive measures, PLCs may encounter issues due to various reasons such as electrical interference, software bugs, communication errors, or component failures. This is where troubleshooting comes into play. Troubleshooting is the systematic process of identifying, diagnosing, and rectifying problems within a PLC system. It requires a deep understanding of PLC architecture, programming logic, signal flow, and communication protocols. An effective troubleshooting approach can minimize downtime and rapidly restore normal operations, saving valuable time and resources for industries.
This guide delves into the realms of preventive maintenance and troubleshooting for PLCs, equipping maintenance personnel, engineers, and technicians with the knowledge and tools needed to ensure the smooth operation of PLC systems. From exploring the importance of regular maintenance to providing insights into common PLC issues and their resolutions, this guide aims to empower individuals with the skills to maintain, troubleshoot, and optimize PLCs in various industrial environments. By embracing these practices, industries can mitigate risks, bolster productivity, and uphold the reliability of their automated processes in an increasingly dynamic technological landscape.
Components of Preventive Maintenance
Preventive maintenance is a systematic approach to ensuring the operational reliability, longevity, and optimal performance of equipment, machinery, and systems. When it comes to Programmable Logic Controllers (PLCs), implementing an effective preventive maintenance plan is essential to avoid unplanned downtime and disruptions in industrial processes. The success of such a plan relies on several key components that collectively contribute to the overall health and functionality of PLC systems.
1. Regular Inspections: Scheduled visual inspections are the cornerstone of any preventive maintenance strategy. Technicians and maintenance personnel should regularly inspect PLC components, including power supplies, input/output modules, communication interfaces, wiring, and connectors. These inspections help identify signs of wear and tear, corrosion, loose connections, or other physical issues that might impact the system’s performance.
2. Cleaning and Housekeeping: A clean environment is crucial for the smooth operation of PLCs. Dust, debris, and contaminants can accumulate over time, leading to overheating, short circuits, and other problems. Regular cleaning of PLC cabinets, components, and surrounding areas prevents such issues and ensures proper ventilation and cooling.
3. Firmware and Software Updates: PLC manufacturers often release firmware and software updates that address bugs, security vulnerabilities, and performance enhancements. Keeping the PLC’s firmware and programming software up to date helps maintain compatibility with new technologies, improves system stability, and safeguards against potential security threats.
4. Lubrication and Mechanical Maintenance: In cases where the PLC system interacts with mechanical components such as conveyors or motors, lubrication and mechanical maintenance are vital. Lubricating moving parts, checking for misalignments, and verifying proper mechanical functioning can prevent breakdowns caused by mechanical issues.
5. Backup and Documentation: Regularly backing up PLC programs and configurations is a fundamental aspect of preventive maintenance. In the event of a system failure or hardware malfunction, having up-to-date backups ensures that the system can be quickly restored to its previous state. Additionally, maintaining comprehensive documentation, including wiring diagrams, programming logic, and system layouts, aids in troubleshooting and quick recovery.
6. Environmental Considerations: PLCs are often deployed in various industrial settings, each with its own environmental challenges. Assessing factors such as temperature, humidity, vibration, and exposure to chemicals is essential. Implementing measures to mitigate the impact of adverse environmental conditions can significantly prolong the life of PLC components.
7. Predictive Techniques: Incorporating predictive maintenance techniques, such as vibration analysis, thermography, and oil analysis, can help detect potential issues before they lead to failure. These techniques rely on data and analytics to identify anomalies and patterns that may indicate impending problems.
8. Training and Skill Development: Maintenance personnel and technicians should receive regular training to stay updated on the latest advancements in PLC technology, maintenance practices, and troubleshooting techniques. Well-trained staff can proactively identify and address issues, reducing the likelihood of system failures.
By integrating these components into a well-structured preventive maintenance plan, industries can ensure the reliability, efficiency, and longevity of their PLC systems. Such an approach minimizes unplanned downtime, increases operational efficiency, and contributes to the overall success of industrial processes.
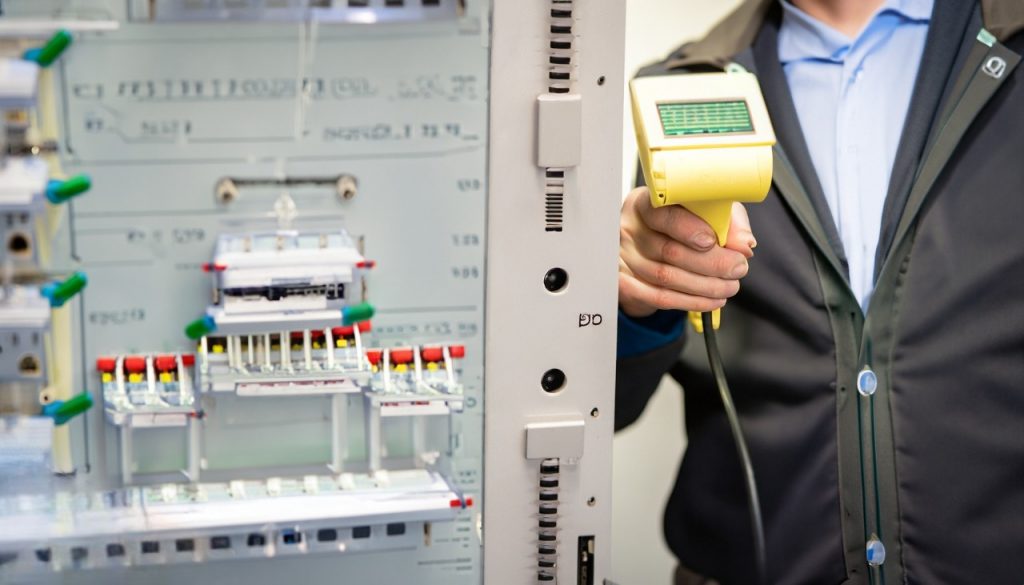
Troubleshooting of PLCs
Troubleshooting is a crucial skill for maintaining the functionality and reliability of Programmable Logic Controllers (PLCs) within industrial processes. As PLCs control a wide range of operations, from manufacturing to energy management, identifying and rectifying issues promptly is essential to minimize downtime and maintain optimal efficiency. Successful troubleshooting involves a systematic approach that combines technical knowledge, logical reasoning, and problem-solving skills.
1. Understanding PLC Operation: A solid foundation in how PLCs function is vital for effective troubleshooting. Understand the scan cycle, input and output processing, ladder logic execution, and communication protocols. This understanding provides insight into how a PLC processes information and controls the equipment it’s connected to.
2. Gathering Information: Start by collecting information about the problem. Talk to operators or technicians who may have observed the issue. Note any error messages or abnormal behaviors in the system. This information can guide your investigation and help narrow down potential causes.
3. Isolating the Problem: Segment the system to narrow down the problematic area. Isolate individual input/output modules, devices, or sections of the ladder logic. By identifying the specific area where the issue arises, you can focus your troubleshooting efforts.
4. Checking Hardware: Inspect physical components such as wiring, connectors, power supplies, and modules. Loose connections, damaged cables, or faulty components can often be the root cause of problems. Use multimeters or diagnostic tools to test voltages, currents, and signals at various points within the system.
5. Reviewing Ladder Logic: Examine the ladder logic or programming code related to the malfunctioning part of the system. Look for logic errors, incorrect conditions, or missing rungs that might lead to unexpected behavior. Compare the logic against the intended control sequence to identify discrepancies.
6. Monitoring Inputs and Outputs: Use monitoring tools to observe input and output signals in real-time. Verify that input signals are correctly reaching the PLC and that outputs are responding as expected. Comparing actual signal values to the intended values can reveal discrepancies.
7. Debugging Software: If the issue lies in the PLC’s programming, use debugging tools provided by the programming software. Set breakpoints, watch variables, and step through the program execution to identify where the logic might be going astray.
8. Communication Diagnosis: If the PLC communicates with other devices or systems, verify the communication pathways. Check network connections, protocols, and addresses. Communication errors can lead to loss of data or disrupted control sequences.
9. Documentation and Record Keeping: Maintain a detailed record of your troubleshooting process, including the steps you’ve taken, the observations you’ve made, and the actions you’ve performed. This documentation can be invaluable if the issue recurs in the future or if other technicians need to continue the troubleshooting process.
10. Collaboration and Expertise: Don’t hesitate to seek help from colleagues, PLC manufacturers’ support, or online forums. Sometimes, a fresh perspective can uncover solutions that you might have overlooked.
11. Testing Solutions: After identifying a potential solution, test it in a controlled environment before implementing it on the production floor. This minimizes the risk of introducing new issues.
Effective troubleshooting of PLCs requires a combination of technical expertise, analytical thinking, and patience. By systematically following these steps and leveraging your understanding of PLCs, you can efficiently identify and resolve issues, ensuring the seamless operation of industrial processes and minimizing production disruptions.
Conclusion
In the realm of industrial automation, where efficiency, reliability, and safety are paramount, the roles of preventive maintenance and troubleshooting in maintaining the functionality of Programmable Logic Controllers (PLCs) cannot be overstated. This journey through the world of PLCs has highlighted the critical importance of proactive measures and systematic approaches to ensure uninterrupted operations and optimal performance.
Preventive maintenance emerged as a fundamental pillar in the pursuit of operational excellence. Regular inspections, cleaning, and firmware updates lay the groundwork for extending the life of PLC components and safeguarding against unexpected failures. The emphasis on environmental considerations, backup strategies, and predictive techniques demonstrated how a well-rounded approach can mitigate risks and enhance the longevity of PLC systems.
On the other hand, troubleshooting illuminated the art of identifying, diagnosing, and rectifying issues that inevitably arise in complex automated systems. From understanding PLC operations and gathering information to isolating problems and collaborating with peers, the systematic process outlined here empowers professionals to overcome challenges efficiently. The blend of technical expertise, logical reasoning, and meticulous documentation ensures that every problem becomes an opportunity for growth rather than a stumbling block.
Collectively, the lessons on preventive maintenance and troubleshooting underscored that success in managing PLCs requires a harmonious fusion of knowledge, skill, and vigilance. As industrial processes become increasingly intricate and technologically advanced, the mastery of these practices becomes a cornerstone for industries striving to remain competitive, adaptive, and sustainable in a fast-paced world.
By embracing the principles of preventive maintenance, industries can preemptively tackle issues before they disrupt operations, thereby saving valuable time, resources, and reducing downtime. Similarly, a robust troubleshooting strategy can mean the difference between swift issue resolution and prolonged disruptions. Both these elements contribute not only to the smooth functioning of PLCs but also to the overall efficiency and profitability of industrial endeavors.
World of PLCs is a dynamic landscape that demands vigilance, adaptability, and expertise. As technology continues to evolve, those who engage in the continuous learning of preventive maintenance and troubleshooting methodologies will be best positioned to harness the power of automation while maintaining control over their processes. With a commitment to excellence and a foundation of knowledge, the path to mastering PLCs becomes an exciting journey of discovery and achievement.